U.T.3.- Gestión de recursos de fabricación en carpintería y mueble.
U.T.3.- Gestión de recursos de fabricación en carpintería y mueble.
Caso práctico
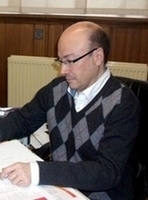
El tío Fernando, viendo los problemas que tiene para sacar adelante su empresa de carpintería, se da cuenta que no está haciendo las cosas bien y tiene que ser más efectivo.
Por el tamaño de su empresa, su almacén no tiene las mismas dimensiones que el de una gran empresa, además lo tiene lleno de productos que no sabe cuando utilizará, algunos de esos productos ni siquiera sabe si algún día llegará a utilizarlos.
En la parte de la empresa dedicada a la fabricación le ocurre algo parecido, lleva muchos años en el mundo de la carpintería y tiene máquinas que apenas usa. En muchas ocasiones ha pensado por qué las compró y si en ese momento fue consciente del poco uso que les iba a dar, ahora se plantea porqué las compró.
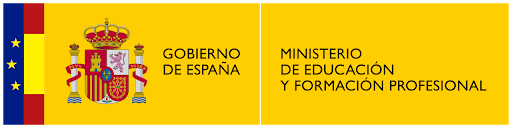
1.- Gestión de materiales en fabricación de carpintería y mueble.
Caso práctico
Ante la situación actual, Fernando sólo piensa; ¡Cuánto desearía tener en dinero líquido el valor de toda esa materia prima que tengo en el almacén! Piensa lo beneficioso que sería ahora tener el dinero que cuesta toda esa materia prima que tiene en el almacén y no va a utilizar y todas aquellas costosas máquinas que no utiliza apenas.
Pero ahora no vale la pena lamentarse, no puede dar marcha atrás en el tiempo y tiene que afrontar el problema y buscar una solución. Fernando lo tiene claro, hay que hacer algo para remediar la situación.
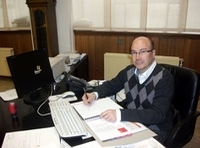
La acumulación de stock en un sistema productivo siempre es negativa para la productividad. En el único caso en el que se puede reportar algún beneficio directo para la empresa, es si se puede especular con él, por ejemplo, las empresas madereras pueden obtener beneficios comprando materia prima para luego venderla cuando su cotización suba. En cualquier otro caso el acopio de material siempre será perjudicial para la empresa, ya que ocasiona múltiples gastos.
Los argumentos que escucharás para justificar la existencia de almacenes son:
- Permiten dar solución a problemas en la fábrica: trabajando contra almacenes de producto semielaborado o terminado se cubren muchas deficiencias en la planificación, mantenimiento.
- El stock ayuda con los tiempos de parada por avería: el que la máquina esté averiada pasa a un segundo plano, el stock hace de regulador y permite mantener constante el ritmo.
- Enmascara el absentismo: al trabajar con un alto nivel de stock, el impacto del absentismo se reduce sustancialmente.
- Se reducen las consecuencias de los defectos de fabricación: con altos niveles de stock es muy fácil fabricar más unidades que las estrictamente necesarias, por lo que retirando las defectuosas, el problema quedará resuelto.
Estos son los argumentos a favor del stock, pero la realidad es otra bien distinta:
- El mantenimiento del stock requiere grandes inversiones: son necesarios almacenes, personal, elementos de transporte.
- El esfuerzo financiero para mantener un elevado volumen de stock llega a ser muy elevado: a cambio de este stock sólo se consigue falta de liquidez.
- Los stocks son siempre fuente de desperdicio encubierto: como la producción sigue funcionando, nadie se pregunta que le pasó a la máquina que se estropeó, por qué no aciertan en las planificaciones, por qué fabrican con defectos. Además el stock siempre se encuentra acompañado de burocracia, transportes y manipulaciones.
La excesiva existencia de stock pasa una importante factura sobre la productividad de cualquier proceso.
En cualquier caso, el stock es necesario pero es importante llevar un control y una correcta gestión de éste. En los puntos siguientes verás las técnicas necesarias para su correcta gestión.
Autoevaluación
Solución
1.1.- Lista de materiales de fabricación (I).
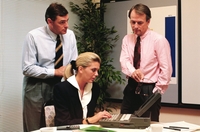
En muchas ocasiones verás que se refieren a la lista de materiales como BOM (Bill of Materials). Para obtener la lista de materiales que forman un producto final, debe efectuarse la llamada explosión de necesidades, que consiste en la descomposición del producto acabado en sus componentes, éstos en otros componentes de los cuales están formados, y así sucesivamente hasta llegar a las materias primas o componentes adquiridos a proveedores ya elaborados.
Puesto que esta descomposición se efectúa para planificar las necesidades de materiales que se necesitan para llevar a cabo los procesos, es importante que un producto se descomponga en los componentes directos que integrarán su proceso de producción, estos componentes se descompondrán en aquellos que se precisarán en su proceso, y así sucesivamente.
El grado de “desintegración” de cada producto o componentes será el que te lleve exactamente a los componentes que se precisen en el momento de producción.
Debes conocer
A continuación tienes una descomposición sencilla de materiales o BOM de un cajón de madera.
La estructura de la lista de materiales debe cumplir los siguientes requisitos:
- Cada componente o material que interviene debe tener asignado un código que lo identifique de forma inequívoca: un código para cada elemento y a cada elemento se le asigna un código distinto.
- Debe realizarse un proceso de racionalización por niveles. A cada elemento le corresponde un nivel en la estructura de fabricación de un producto, asignado en sentido descendente.
El nivel asignado a un elemento es el más bajo que le corresponde según el árbol de fabricación de todos los productos a los que pertenece. En el ejemplo sólo se ha considerado un producto final y se ha descompuesto de una forma muy sencilla obviando los sistemas de unión, pero la codificación de nivel inferior ha de realizarse estando descritas las listas de materiales de todos los productos que intervienen en la fabricación bajo supervisión del sistema de programación y control de la producción.
1.1.1.- Lista de materiales de fabricación (II).
Para que las listas de materiales faciliten que el sistema de programación y control satisfagan sus objetivos, aquí tienes las características que debe tener la base de datos a que da lugar el conjunto de listas de materiales:
- Las listas deben estructurarse para facilitarla introducción de nuevas opciones en los productos finales que intervienen en el programa maestro, que es el programa que marca las directrices y política de empresa a seguir. El catálogo de productos de una empresa suele variar continuamente, por la sustitución de unos productos por otros, eliminación de productos, incorporación de otros nuevos y, lo que es más frecuente, ampliación de la gama de productos mediante la introducción de nuevas opciones a los ya existentes.
En cualquier caso, deben mantenerse listas de productos finales, pero con el fin de facilitar la programación indicada por el plan final de montaje, tanto, cuando la producción se realiza en un entorno de fabricación sobre pedido, como es el caso de la pequeña y mediana industria de la carpintería y mueble, como cuando existe una gran gama de opciones.
- La lista de materiales debe mantenerse actualizada, incluyendo información sobre los plazos de producción para cada operación de fabricación y sobre los de aprovisionamiento en el caso de materiales o componentes que se adquieren a proveedores externos. Asimismo, debe permitir la realización de estudios para la estimación de costes de producción, (de materiales, de mano de obra directa o indirecta y de imputación de costes generales).
En resumen, las listas de materiales deben constituir el núcleo fundamental del sistema de información en el que se sustenta el sistema de programación y control de la producción.
Han de organizarse para satisfacer de forma inmediata todas las necesidades del mismo, incluyendo la de facilitar el conocimiento permanente y exacto de todos los materiales que se emplean en la fabricación, los plazos de producción, su coste y el control de las existencias. En definitiva, todos los aspectos que intervienen en las decisiones cotidianas en las que se concreta el programa de producción.
Si se realiza una buena gestión de las listas de materiales se obtendrán las siguientes ventajas:
- Gestión más efectiva de los costes de desarrollo y fabricación.
- Definiciones de productos más completas a lo largo del ciclo de vida.
- Aumento de la productividad de los equipos.
- Posibilidad de comprobar si el producto creado se corresponde con la intención del diseño; comparación de las distintas listas de materiales durante la fase de creación; y captura de registros de creación para la gestión de resultados de pruebas, informes de cumplimiento de normativas y soporte de verificación de la garantía.
- Mejora de la colaboración entre personas y equipos.
- Mejora de la planificación empresarial conciliando y agregando la información fundamental.
Autoevaluación
1.2.- Teorías para gestionar el stock de materias primas.
Poder controlar la cobertura de stocks es un punto fundamental dentro de la gestión de la planificación de materiales.
El stock te sirve para:
- Anticiparte a la demanda.
- Cubrir las fluctuaciones de la demanda y suministro.
- Beneficiarte de descuentos ofertados por proveedores.
- Cubrir el tiempo necesario para mover materiales de un lugar a otro de la cadena de suministro.
- Protegerte contra las fluctuaciones de precio del mercado.
Sin embargo, al igual que la acumulación de stock te ayudará a mejorar tu servicio, también puede perjudicarte muy negativamente en forma de costes:
- Asociados a su producción.
- Asociados a su transporte.
- Asociados a su almacenamiento.
- Asociados a su obsolescencia.
Para evitar los efectos negativos del stock, a continuación se exponen los sistemas de gestión de procesos más utilizados en la actualidad:
- Sistema MRP (Material requirement planning).
Este sistema es propio de la gestión tradicional; es utilizado hoy en día como sistema de planificación para la producción, lo que le ha valido que sea aplicado también en sistemas más avanzados e incluso en combinación con el sistema Kanban, que verás a continuación.
El sistema MRP calcula la cantidad a producir de cada componente en función del consumo previsto a partir de la explosión final y el momento del consumo a partir de los leads times de cada proceso. El lead time es el tiempo que transcurre desde que la primera pieza entra en el proceso de producción, hasta que está terminada la última, es el tiempo que consume fabricar un lote de proceso completo.
A continuación tienes un esquema de su funcionamiento:
- Sistema Kanban:
Este sistema es propio de la gestión Just In Time, que advierte a un proceso que material necesita el proceso que sigue, en qué cantidad y momento, mediante una tarjeta o similar. El sistema está dirigido muy especialmente a evitar despilfarros en el sistema productivo, en forma de tiempos de producción y stock innecesarios. Concretamente persigue fabricar exactamente lo que se necesita y justo cuando se necesita. A continuación tienes un esquema de funcionamiento del sistema Kanban.
- Sistema TOC:
Está basado en la gestión de las limitaciones o cuellos de botella, se gestiona de forma que la primera operación del proceso envía material ya procesado a la segunda al ritmo que pueda absorber la operación del proceso con menor capacidad, incluyendo el proceso o cliente que deba recibir el producto final; de esta forma se asegurará el avance del producto sin demoras, ya que todas las operaciones procesarán el producto por debajo de su capacidad, excepto el cuello de la botella, que por tanto no podrá absorber ningún desequilibrio suyo o de las operaciones anteriores por lo que dispone un stock ante ella para que no pare, pase lo que pase.
1.3.- Stock mínimo y de seguridad en el proceso de fabricación.
Los niveles de stock son aquellas cifras que indican las cantidades de cada artículo, que deben guardarse para atender de manera satisfactoria la demanda. Estos artículos y materiales deben ser concentrados y almacenados en sus respectivos almacenes, guardando y cumpliendo con todas las normas de seguridad establecidas. Como sabes una gran desventaja y factor limitante son las limitaciones de espacio, el capital financiero y el ritmo de empleo de los materiales si no se cuenta con un análisis de rotación.
Se pueden definir los siguientes tipos de stock:
- Stock mínimo:
Es aquella cantidad de materias primas o materiales que necesita la línea de producción o la línea de servicio para satisfacer su demanda, mientras espera la llegada de los productos. Este nivel mínimo supone el límite inferior de existencias dentro del cual no se debe bajar.
El concepto de stock mínimo está íntimamente relacionado con el consumo de un material en un tiempo determinado, y el tiempo de reposición que estimas para la llegada del producto.
Cálculo del stock mínimo:
Sm= C x T
Siendo: Sm = stock mínimo.
C= consumo de producto en días.
T = tiempo de reposición en días.
Los tiempos de reposición deben estar establecidos por cada unidad.
- Stock de seguridad:
Es el previsto para demandas inesperadas de clientes o retrasos en las entregas de proveedores. El stock de seguridad sería el stock mínimo más un porcentaje de seguridad. Este porcentaje depende de la política de la empresa.
Cálculo del stock de seguridad:
Ss= Sm + %
Siendo: Ss= stock de seguridad.
Sm = stock mínimo.
%= porcentaje de seguridad.
Normalmente el porcentaje de seguridad es un 10 %.
Es necesario que sepas que existen también otros tipos de stock:
- Stock standard:
Es aquel que se mantiene habitualmente en la empresa para satisfacer los requerimientos de la demanda de productos por parte de los clientes.
- Stock máximo:
Corresponde al máximo nivel de stock que puede tener almacenado una empresa de una existencia, esto desde un punto de vista técnico, administrativo y económico. El punto técnico se basa en la capacidad de producción, el administrativo sobre una organización administrativa y el punto económico porque el coste de manutención de un stock excesivo es altísimo y no aporta valor a la operación.
Autoevaluación
Solución
2.- Gestión de procesos.
Caso práctico
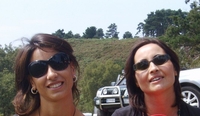
Ana estaba en el almacén haciendo un recuento de los materiales que tenía allí acumulados su tío y que ella entendía que no se iban a utilizar. Había almacenados muchos productos a los que no creía que pudiese dar salida, así que estaba pensando qué hacer al respecto.
Ana, vista la situación, le cuenta a su amiga Clara si le puede echar una mano para aprender a calcular el stock, el lote óptimo de fabricación y Clara se ofrece a ayudarle para encontrar una solución. También le comenta que trabaja en una empresa de muebles como administrativa y puede ayudarles.
En el punto anterior has visto cómo calcular el stock mínimo y de seguridad. En este verás cómo se calcula el lote óptimo de fabricación y el lote óptimo de transferencia.
Los parámetros con los que se trabaja para hallar estos lotes son:
- Q: volumen de producción que se quiere fabricar.
- Cs: costes por unidad de volumen de mercancías y de tiempo.
- Cp: coste de lanzamiento y preparación de la producción de un lote de proceso.
- Ct: coste de transferir un lote hasta la siguiente operación.
Se operará con “m” lotes de proceso y “n” de transferencia en cada una de las operaciones; se trata de determinar el lote económico de una operación del proceso.
El tamaño del lote del proceso será q, q=Q/m, y tienes el tienes el tiempo T disponible para fabricar el volumen de producción que se quiere fabricar, Q. el coste total de la operación (CT) será:
Donde t es el tiempo que deberá soportar este coste:
Sustituyendo en la ecuación anterior se tiene que:
Lote de fabricación: es una unidad de medida de fabricación que se planifica y fabrica con referencia a un número.
Lote de transferencia: puede no ser, y de hecho muchas veces no debe ser, igual al lote de fabricación o proceso. El lote de transferencia es el que se utiliza para transportar artículos entre dos centros de trabajo.
2.1.- Lote óptimo de fabricación.
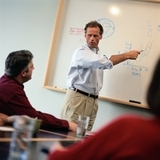
El mínimo valor del coste se obtendrá a partir de las variables q (tamaño de proceso óptimo) y n (número de lotes de transferencia). Igualando a cero las ecuaciones parciales de CT respecto a ambas variables, se tienen las siguientes expresiones:
Número de transferencia óptimo:
Lote de proceso óptimo:
Combinando estas dos ecuaciones puedes calcular el tamaño del lote de transferencia:
Ejercicio resuelto
Datos de partida:
Volumen a producir = 50000 unidades.
Tiempo disponible para fabricar = 1 año.
Coste de mantenimiento del stock por unidad de mercancía y tiempo = 500 € / unid año.
Coste de lanzamiento y preparación de un lote = 1000 €.
Coste de evacuar cada lote de transferencia hasta la siguiente operación = 100 €.
Con estos datos el tamaño del lote de proceso óptimo será:
Y el tamaño del lote de transferencia será:
Las 50.000 piezas se lanzarán a fabricar en lotes de 447 piezas, y cada uno de esos lotes se transfiere en 3 lotes de transferencia, es decir, cada lote de transferencia tendrá 141 piezas o el entero más cercano hasta completar el lote.
3.- Equilibrado de líneas de fabricación.
Caso práctico
Fernando ha aceptado la ayuda de su sobrina para reestructurar el método de fabricación, dos cabezas piensan mejor que una.
Ella le comenta a su tío que debe organizar bien los trabajos, él lleva mucho tiempo en el negocio y seguro que sabe el tiempo que se tarda en realizar cada tarea, ahora sólo tiene que organizar los trabajos de una forma equilibrada para que ocupen el mismo tiempo dentro de un ciclo y así aprovecharlo al máximo.
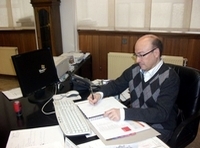
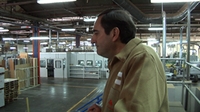
Para un adecuado empleo de los recursos del sistema de producción se hace necesario que haya un equilibrio en las cargas de trabajo durante la fabricación.
Este equilibrio se consigue con el reparto del trabajo entre los distintos puestos de trabajo o secciones de la empresa, en un ciclo, cada uno de ellos debe ocupar exactamente el mismo tiempo.
Por equilibrado debes entender “la igualdad de producción para cada una de las sucesivas operaciones en la secuencia de un sistema de fabricación”. Pero cuando se trabaja con varios productos, el equilibrado se complica, aunque el método a utilizar es similar.
Para equilibrar la carga de trabajo por producto, las soluciones que pueden adoptarse varían. Se puede desde subcontratar parte del proceso, hasta intensificar la mejora de métodos y procesos en los puestos limitantes.
Si tienes una igualdad de tiempos de producción en todas las etapas, se dice que el equilibrado del sistema es perfecto, pero si no es el caso el ritmo de la producción viene marcado por la etapa más lenta o con menos capacidad, el resto de las etapas que componen el sistema originarán desperdicio de mano de obra y aumento de stock en proceso. Esto se tiene muy en cuenta en la fabricación en cadena, como por ejemplo en la fabricación de puertas.
El problema de equilibrado de la producción puede ser objeto de varios planteamientos, según las circunstancias de cada caso. Aunque se puede llegar a dos únicos planteamientos generales:
- Partir de la demanda dada por el mercado y combinar todos los factores a tu disposición para conseguir el nivel de producción exigido.
- Con los recursos que dispones y la combinación de estos calcular la demanda que puedes atender.
Autoevaluación
Solución
3.1.- Método equilibrado.
Para proceder a realizar la implementación de una cadena de producción es condición indispensable conocer el producto y sus componentes así como las máquinas y útiles necesarios para el montaje de dicho producto.
A continuación, debes cronometrar el tiempo total de montaje que lleva el producto, teniendo en cuenta:
- Prioridades y secuencia de las tareas elementales.
- Cronometrar por separado las tareas elementales.
- Útiles y máquinas que intervienen en la realización de cada tarea elemental.
Se construye un diagrama de prioridades. Vas a verlo mediante la utilización de un ejemplo que representa una cadena de producción con 5 puestos de trabajo (P1, P2, P3, P4, P5) con un trabajador cada uno de ellos y en los que su ciclo de trabajo es el que se indica en el diagrama.
Viendo el diagrama se observa que:
- Para realizar las tareas de los puestos P2 y P4 se debe haber realizado previamente la tarea del P1.
- Para realizar las tareas del puesto P3 se debe haber realizado las del puesto P2.
- Los puestos P2 y P3 trabajan en paralelo con el P4.
- Los procesos de los puestos P4 y P3 deben haber concluido antes de poder comenzar a realizar los puestos del P5.
A continuación verás algunos conceptos que te ayudarán a la hora de dictaminar un veredicto sobre el grado de aprovechamiento de la cadena:
Coeficiente equilibrado. Es el porcentaje de inactividad medio de los componentes de la línea. Para calcularlo se aplica la siguiente fórmula:
Siendo: N = el número de operarios.
Cp = ciclo de los distintos operarios, es decir el tiempo que tarda cada operario en realizar su trabajo sobre una unidad.
Cl = ciclo limitante, es el ciclo más extenso en tiempo dentro de todo el proceso.
D = coeficiente equilibrado, es el tiempo que los trabajadores están sin realizar ninguna actividad dentro de la cadena, expresado en porcentaje.
Eficiencia de la cadena. La cual mide el grado en el que se aprovecha la mano de obra de la que se dispone, este dato también se expresa en tanto por cien.
Siendo: E = eficiencia de la cadena.
Cp = ciclo de los distintos operarios.
N = número de operarios.
Cl = ciclo limitante.
Rellenando ambas fórmulas, con los datos del diagrama de ejemplo, puedes estudiar en qué grado se aprovecha la capacidad de producción de la cadena.
Como puedes ver el aprovechamiento de la cadena es de poco más del 50 % y la inactividad de la cadena es casi del 50%. Se puede decir que se está produciendo la mitad de lo que se podría llegar a producir.
3.2.- Directrices de equilibrado.
Las decisiones que tomes sobre el equilibrado debes orientarlas a intentar reducir el ciclo de la sección limitante, es decir la tarea que hace que las tareas sucesivas se retrasen, hasta conseguir un aprovechamiento de la cadena alto. Tu fin debe ser alcanzar una eficacia de la cadena de un 100 %. Aunque sea difícil de conseguir, nunca te conformes con un porcentaje menor.
Antes de aplicar las directrices, debes conocer a la perfección el método de producción. A continuación tienes unas directrices a seguir para reducir el ciclo de una operación:
- Dividir la tarea: ¿se puede dividir la tarea de manera que las unidades puedan ser procesadas en dos estaciones de trabajo? En este caso se repartiría el trabajo entre varios puestos de trabajo.
- Compartir la tarea: ¿una tarea podría compartirse de manera tal que un puesto adyacente realice parte del trabajo? Esta operación difiere de la opción anterior porque en este caso se trata de crear una estación adyacente de apoyo.
- Utilizar estaciones de trabajo paralelas: puede ser necesario dado el alto grado de saturación de una sección, en la que tengas que asignar el trabajo a dos o más estaciones para que trabajen de forma paralela. Esta técnica consiste en duplicar los puestos de trabajo, y se conoce como NAGARE.
- Horas suplementarias de trabajo: en casos en los que el desequilibrio sea muy grande se puede aumentar las horas de trabajo de una sección o incluso duplicar turnos.
- Rediseño: en algunos casos nos veremos obligados a rediseñar el producto para intentar reducir el tiempo de la tarea.
En base al ejemplo propuesto en el punto anterior se tomarían las siguientes medidas:
- Se unificarían las operaciones de los puestos P2 y P3 dado su baja saturación, creando un puesto de trabajo que se llamaría P23, y que tendrá un ciclo de trabajo de 30 segundos. Con esta operación se crea un puesto de trabajo con un ciclo más alto lo que implica una mayor saturación y además con u operario menos.
- El operario libre se podrá utilizar para duplicar el puesto P4 que es el más saturado. De esta manera se logra reducir el ciclo de este puesto.
Una vez realizados los cambios la situación es la siguiente:
Con la situación actual los aprovechamientos de la cadena de producción serían los siguientes:
Coeficiente de equilibrado:
Eficiencia de la cadena:
Como puedes ver el grado de aprovechamiento de la cadena ha aumentado de forma considerable.
4.- Planificación de la producción.
Caso práctico
Ana y su tío siguen pensando cómo solucionar los problemas por los que atraviesa la empresa.
Ana le explica a su tío que debe reducir el stock al mínimo, este sabe que Ana tiene razón, toda esa materia prima que tiene almacenada y que posiblemente no utilice es fruto de un stock excesivo.
Para alcanzar un nivel de stock apropiado a las necesidades de la empresa es preciso que hagan una planificación. Ana le comenta a su tío que para planificar existen varios sistemas.
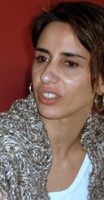
La gestión eficiente de los procesos de producción pasa por reducir al mínimo los stocks, siempre teniendo en cuenta la demanda, esto se consigue sincronizando las operaciones, transfiriendo los materiales de una a otra justo en el momento en el que la segunda los precisa.
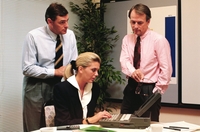
Se trata de desarrollar una planificación más eficiente que los modelos de gestión de stocks para controlar los materiales que forman parte de los procesos de producción. Buscando planificaciones directamente relacionadas con las necesidades de las distintas operaciones y no constituidas por “lotes económicos”, cuya cuantía está más relacionada con los costes del nivel de existencias.
Los sistemas de gestión de materiales para los procesos se ocupan de que los materiales, componentes y productos estén disponibles siempre en la clase, cantidad y momento en que son requeridos.
El Kanban y MRP son dos métodos de gestión de materiales que intentan solucionar la planificación y envío de materiales y productos de forma que se consiga adaptar la producción a la demanda, pero utilizando principios distintos.
El sistema MRP (Material Requirement Planning) opera en base a la planificación de las necesidades de materiales. Actúa con filosofía de sistema “push” (empujar), a partir del programa maestro de producción. Con él y la lista de materiales, la ruta de fabricación y los datos de centros de trabajo e inventarios, efectúa el proceso de explosión de necesidades considerando que la capacidad es infinita y que los lotes y plazos de fabricación son constantes.
Pero en un sistema “push” las necesidades son cubiertas antes de que realmente se produzcan, es decir, los componentes y productos deberán estar listos antes de que sean demandados, lo que podrá suponer un aumento de los stocks. Con el sistema MRP, si un cliente hace un pedido de 50 unidades de puerta, la empresa tiene un stock de puertas suficiente para cubrir esa demanda, siempre y cuando esté dentro de los niveles normales de demanda de la empresa.
El sistema Kanban, por otro lado, funciona como un sistema “pull” (arrastre o tirón), siendo los “procesos clientes” quienes determinen aquellos elementos que sus respectivos “procesos suministradores” deban proporcionar, en cantidad, clase y plazo de entrega. En un sistema tipo “pull” las necesidades serán cubiertas después de ser constatadas. El sistema Kanban proporciona gran flexibilidad al sistema, pero no determina la producción en base a una planificación. Con este sistema cuando un cliente hace un pedido de 50 unidades de puerta, se comienzan a fabricar esas unidades para que puedan ser entregadas en el plazo previsto.
Autoevaluación
Solución
4.1.- El sistema MRP.
El sistema pretende conocer: ¿Qué materiales son requeridos? ¿Cuánto se necesita de cada material? ¿Cuándo es requerido cada material? El problema fundamental no es vigilar los niveles de stock, sino asegurar su disponibilidad en la cantidad deseada, en tiempo y lugar adecuado.
El sistema MRP parte de un plan maestro de producción (PMP) previamente confeccionado y que determina cuándo debe fabricarse el producto final y en qué cantidad y a partir de él van deduciéndose las necesidades de material y componentes.
Los objetivos que busca el sistema MRP son:
- Asegurar la entrega de los artículos finales en las fechas establecidas en el PMP.
- Establecer un programa de lanzamientos de pedidos que garantice el mínimo nivel posible de stocks.
Al utilizar el sistema MRP, el programa maestro proporciona órdenes de compra por materias primas y órdenes de fabricación para taller. El proceso de detallar las partes determina todos los componentes necesarios para fabricar un producto específico. Este proceso de detalle requiere de una lista completa de materiales que incluya cada una de las partes necesarias para manufacturar el artículo final en el programa maestro.
En el proceso de detalle de partes es necesario considerar los inventarios, es decir las cantidades disponibles de cada artículo que ya se tienen o están pedidas y por diferencia, las cantidades que deben comprarse. Por ejemplo, una orden de 100 artículos finales puede requerir un nuevo pedido de únicamente 20 piezas de una materia prima debido a que 50 piezas ya están en el almacén y 30 piezas están pedidas.
Elementos del MRP:
Para cumplir los objetivos que este método tiene planteados se necesita una serie de datos iniciales sobre los que actúa el algoritmo MRP:
-
Plan maestro de producción (PMP): es el documento que refleja para cada artículo final, las unidades comprometidas así como los periodos de tiempo para los cuales han de tenerse terminados.
Normalmente los periodos temporales son de una semana con un horizonte temporal que debe ser lo suficientemente amplio como para que abarque al menos todos los pasos de fabricación. No obstante, depende del tipo de producto que se trabaje. En la industria de la carpintería y mobiliario, periodos temporales de una semana suelen ser adecuados.
-
Lista de materiales (BOM): es necesario conocer para cada artículo su estructura de fabricación, en donde quedan reflejados los diferentes elementos que lo componen, así como el número necesario de cada uno de esos elementos para fabricar una unidad de este artículo.
-
Fichero de registros de inventarios: si se dispone en almacén de unidades suficientes de alguno de los componentes necesarios, no tendría sentido volver a pedirlos o fabricarlos. Por ello es necesario conocer de cada componente y artículo su nivel actual de existencias, así como los pedidos ya realizados pendientes de recibir, la política de pedido para cada uno (stock de seguridad y tipo de lote), y el tiempo de suministro o fabricación. El tipo de lote indica cómo han de hacerse los pedidos.
4.2.- Planificación de necesidades de material MRP.
En la planificación de necesidades, una vez que tienes desarrollada la lista de materiales debes tener en cuenta:
- La unidad de medida para el Lead Time (segundos, horas, días.)
- Periodo base de planificación de la producción, que debe coincidir en unidades con el Lead Time.
- Número de periodos a planificar.
Las magnitudes calculadas en el desarrollo del MRP son:
- Necesidades brutas: volumen de componentes o materiales que debes tener disponibles al final de un periodo para el proceso siguiente.
- Stock previsto: volumen de componentes o materiales que se prevé que quedarán en forma de existencia al final de un periodo. Esto es debido a que el lote de producción no coincide con alguna de las necesidades brutas anteriores.
- Necesidades netas: volumen de componentes o materiales que habrá que obtener para disponer de las necesidades brutas al final del periodo.
Estas magnitudes tienen la siguiente relación:
Necesidades netas = Necesidades brutas - Stock previsto.
(Lo que tengo que fabricar = lo que necesito – lo que tengo).
Después de este cálculo, las órdenes de trabajo deben de lanzarse teniendo en cuenta su LT (Lead Time), para poder cumplir con la programación. A continuación se resume las etapas necesarias para poder aplicar el sistema MRP:
A continuación se muestra un ejemplo de MRP para una puerta. Se ha simplificado el sistema real de fabricación, con el fin de tomar un ejemplo válido para el objeto que se busca:
Como puedes ver el Lead Time (LT) de la fabricación es de 5 días desde que se realice el pedido de materias primas hasta que puedas expedir tu producto terminado.
4.3.- El sistema MRP II.
El sistema de planificación de las necesidades de materiales (MRP) puede llevarse a cabo de una manera más completa si se tienen en cuenta los recursos que se precisa utilizar (humanos y equipamientos) y la capacidad disponible, y esto es precisamente lo que propone el sistema MRP II (Manufacturing Resource Planning).
El sistema MRP, tal y como ha sido expuesto, opera como si la capacidad fuera infinita.
Los puestos de trabajo y sus disposiciones por equipos y carga para el trabajador, pueden limitar las órdenes de producción lanzadas desde el MRP, en cuanto a la capacidad que puede asimilar cada equipo de trabajo. Por lo que, de forma similar a como se han planificado las órdenes del sistema MRP, pueden planificarse órdenes más detalladas, que se refieran primero a la necesidad de materiales y seguidamente se traduzcan en cargas para cada puesto de trabajo y la duración del ciclo correspondiente, a fin de adaptar la configuración de dichos centros hasta donde sea posible, y a partir de ahí modificar las órdenes de lanzamiento para adaptarlas a la capacidad, lo que podrá suponer replantear el plan maestro de producción.
Existe la posibilidad de poder ensayar las modificaciones realizadas en el sistema MRP II a modo de análisis, como por ejemplo:
- ¿Cómo afectaría una variación determinada en las ventas y con ello en el Plan Maestro de Producción a la planificación de órdenes para la obtención de materiales y a la relación carga-capacidad?
- ¿Cómo afectaría una variación de los leads-time de los distintos materiales o de la capacidad en la planificación de la producción?
Como puedes suponer, es una herramienta muy efectiva para poder decidir el plan de lanzamientos definitivo. La ejecución de órdenes se plantearía ahora de la siguiente manera:
Como puedes observar en la figura de no existir capacidad suficiente se replantearía el plan maestro de producción por retroalimentación de la información relativa a la carga y a la capacidad.
El replanteo del plan maestro de producción que podría tener lugar en caso de existir capacidad insuficiente, transforma el problema del centro de trabajo que tenga la sobrecarga en un problema que sobrepasa sus atribuciones, de forma que recaerá en el responsable de la programación maestra de toda la planta.
Existe otra tabla en la que se compara la capacidad de la fábrica, puesto a puesto, con los recursos que se necesitan. Se llama planificación de necesidades de capacidad.
Autoevaluación
Solución
4.4.- Planificación de necesidades de capacidad CRP.
Para el establecimiento del plan de necesidades de capacidad (capacity requeriments planning = CRP) la base la constituyen las órdenes planificadas.
Partiendo de las planificaciones de producción de producto final y componentes de la tabla de lanzamientos y teniendo en cuenta las necesidades de recursos de la tabla de capacidad por centros de trabajo, pueden obtenerse las necesidades de capacidad para tales centros, para todos los productos y componentes planificados, incluyendo stocks, lead time de obtención y notificación (lo que se hizo inicialmente en el MRP). Para ello será necesario calcular las horas de utilización que necesito para completar el lote y compararlas con las horas disponibles del mismo que tienes.
El plan de necesidades de carga puede utilizarse en dos situaciones:
-
A capacidad infinita: esto significa que la carga requerida se asigna al centro de trabajo sin tener en cuenta si este tiene suficiente capacidad o no. Puede utilizarse una regla alternativa de planificación de forma que cuando la carga supere cierta magnitud, se asigne cierto porcentaje a la semana o mes correspondiente y el resto a la semana o al mes siguiente.
-
A capacidad finita: la carga requerida se asigna al centro de trabajo teniendo en cuenta un límite de carga, en caso de existir sobrecarga existen dos posibilidades, desplazar carga hacia atrás o hacia delante según sea el caso.
En la industria de la carpintería y mobiliario es común aumentar la capacidad, subcontratando procesos en un momento dado, debido al alto coste de las instalaciones y máquinas de fabricación.
De manera general para el plan de necesidades de capacidad se necesitan las siguientes informaciones:
- Plan maestro detallado.
- Un sistema MRP I.
- La base de datos del MRP I, que incluye:
- Lista de materiales.
- Estado de stock.
- Procedimiento de lotificación.
- Plazos de fabricación.
- Los ciclos (metas y tiempos estándar).
- Control de actividades productivas (estados de las órdenes abiertas, puestos de trabajo en que se encuentran: en cola, en proceso, esperando el traslado).
- Parámetros de programación:
- Duración estimada de espera en cada centro.
- Plazos de transferencia intercentros.
Para saber más
Puede que te interese conocer más aspectos del CRP (Capacity Requirements Planning), podrás encontrar más información en los siguientes enlaces:
Autoevaluación
Solución
4.5.- Otros sistemas de planificación de la producción.
Como sabes los sistemas de planificación y control de la producción están formados por un conjunto de niveles estructurados de planificación, que contemplan tanto los planes maestros, la gestión de materiales, así como los niveles de ejecución o gestión de taller.
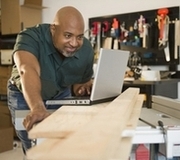
En los últimos años se ha estado produciendo un notable incremento de la importancia que tiene el subsistema de producción en el desarrollo de la actividad empresarial. Los sistemas de gestión de la producción integran las diferentes funciones de planificación y mando de la producción; a partir de la utilización de técnicas, diagramas, gráficos y software, que facilitan los cálculos y decisiones en torno a la selección de las mejores variantes de la producción.
Además de los sistemas que has visto en los puntos anteriores (MRP y MRP II), existen otros sistemas de planificación de producción:
- JIT (Just in Time), de origen japonés y desarrollado inicialmente por Toyota Motor Co.
- OPT (tecnología de producción optimizada), desarrollada inicialmente por Eliyahu M. Goldratt, que más tarde dio lugar al surgimiento de la Teoría de las Limitaciones (TOC) y a su aplicación (sistema DBR: drum-buffer-rope)
- LOP (Load Oriented Production), control de producción orientado a la carga, sistema desarrollado en Europa Occidental.
La idea básica del JIT es producir artículos necesarios en las cantidades adecuadas y en los instantes de tiempo precisos; esto conduce a lotes de fabricación muy reducidos. Para reducir los tamaños de las series es necesario que los tiempos de puesta a punto de las máquinas sean lo más pequeños posible y la posibilidad de rechazo mínima.
La finalidad del OPT/TOC/DBR, es maximizar el flujo de salida del proceso productivo, el cual es considerado como una red por la que circulan los productos. Un principio fundamental de dicho enfoque, es que solamente son “críticas” las operaciones que representan limitaciones en el sistema y serán aquellas denominadas “cuellos de botella”, y que son los recursos u operaciones que van a determinar el nivel de outputs y facturación del sistema productivo.
LOP, es un sistema desarrollado a partir de 1987 que se emplea en algunas empresas europeas (fundamentalmente alemanas) y que es útil en el control de la actividad de la producción en talleres caracterizados por grupos de celdas productivas o puestos de trabajos los cuales juntos pueden producir una variedad de productos diferentes (producción por orden) y se base fundamentalmente en el control de producción orientado a la carga.
Para saber más
Puede que te interese conocer con más profundidad los sistemas que aparecen en este punto, si es así, puedes encontrar más información en el siguiente enlace:
5.- Control de fabricación.
Caso práctico
Ana sigue trabajando sobre la planificación de producción de la empresa.
Ana ha llamado a su amiga Clara para que le ayude, seguro que por su experiencia les aportará ideas muy útiles. Clara les dice que está muy bien que hayan pensado en planificar la producción, además les explica que realizando un control de la fabricación pueden obtener información muy importante.
Realizando el control de la producción pueden ejecutar simulaciones para ver cuál sería la producción en distintas situaciones y así poder corregir los fallos antes de que se produzcan.
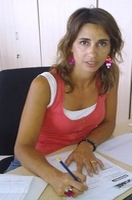
La herramienta MRP sirve como apoyo para determinar diferentes escenarios de producción posible. La producción de la empresa puede planearse cotejando diversas condiciones, para obtener información en distintos campos, como por ejemplo:
- Órdenes de producción.
- Necesidades de componentes.
- Estructura de producto.
- Cantidades.
- Necesidades de abastecimiento.
- Procesamiento por órdenes de compra.
Los sistemas MRP sugieren diferentes acciones sobre el manejo de inventario o variaciones en los procesos, con el fin de aumentar la productividad y planear adecuadamente las necesidades de abastecimiento y manejo de partes.
Con un MRP, puedes simular diversas circunstancias que servirán para determinar las cantidades óptimas de necesidades de materiales y partes. Es posible especificar diversas variables usando un software adecuado y realizando una simulación. El uso de simulaciones por ordenador es muy eficiente, pudiéndose especificar casos muy complicados y que pueden ayudar a la empresa a solucionar los posibles problemas.
Autoevaluación
5.1.- Simulaciones, reprogramación y medidas correctoras.
Como has visto es muy interesante el que la empresa pueda realizar simulaciones, mediante las cuales se podría ver cuál sería la producción en distintos escenarios y situaciones.
Por ejemplo, puede ser muy útil para estudiar la situación de tu sistema productivo, si la demanda aumentase un tanto por ciento. O hasta dónde deberías aumentar tus ventas para poder saturar tu fábrica.
El abanico de opciones que se abre con una herramienta tipo MRP, es prácticamente inagotable. Se pueden dimensionar plantillas, optimizar las compras, estudiar impactos de inactividad o de sobre saturación, dimensionar la duración de jornada laboral en función de una demanda.
Las simulaciones tipo “Que pasa si…” ayudan a desarrollar el mejor plan de producción con el objeto de cumplir con las fechas de entrega con los clientes, teniendo en cuenta la disposición de materiales, disponibilidad de operarios, máquina y utillaje.
El éxito de las empresas industriales depende de su capacidad de responder con rapidez, precisión y consistencia a la siempre cambiante demanda del mercado.
Como es de imaginar el día a día de una industria está sujeto a innumerables imprevistos y todos siempre irán en contra de la rentabilidad de tu empresa. Ante esta situación tan desfavorable sólo las empresas más flexibles y rápidas se adaptarán correctamente a la demanda.
La reprogramación consiste en cambiar las órdenes de trabajo, en función de los imprevistos que surjan.
Debes conocer
A continuación se muestra un ejemplo de una reprogramación:
Autoevaluación
Solución
5.2.- Factores de control de la fabricación.
Existen tres tipos de factores de producción necesarios para lograr que el control de la producción tenga éxito:
- Creativos: son los factores propios de la ingeniería de diseño y permiten configurar los procesos de producción.
- Directivos: se centran en la gestión del proceso productivo y pretenden garantizar el buen funcionamiento del sistema.
- Elementales: son los inputs necesarios para obtener el producto (output). Estos son los materiales, energía.
A continuación verás cada uno de los elementos del sistema de control de la fabricación:
- Producción: se ocupa específicamente de la actividad de producción de artículos, es decir, de su diseño, su fabricación y del control del personal, los materiales, los equipos, el capital y la información para el logro de esos objetivos.
- Operaciones: es un concepto más amplio que el de producción. Se refiere a la actividad productora de artículos o servicios de cualquier organización ya sea pública o privada, lucrativa o no.
La gestión de operaciones, por tanto, engloba a la dirección de la producción.
- Producto: es el nombre genérico que se da al resultado de un sistema productivo y que puede ser un bien o un servicio. Un servicio es una actividad solicitada por una persona o cliente.
- Actividad productiva: producir es transformar unos bienes o servicios (factores de producción o inputs) en otros bienes o servicios (outputs o productos). Producir es también crear utilidad o aumentar la utilidad de los bienes para satisfacer las necesidades humanas.
- Función de producción: es aquella parte de la organización que existe fundamentalmente para generar y fabricar los productos de la organización. La función de producción a su vez está formada por el proceso de transformación, que es el mecanismo de conversión de los factores o inputs en productos u outputs.
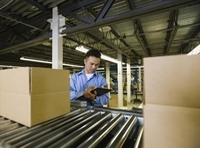
Autoevaluación
Solución
6.- Prevención de riesgos laborales durante el proceso de fabricación.
Caso práctico
Clara sigue colaborando en la elaboración de un plan de gestión y control de fabricación, que le ayude a no volver a cometer los errores del pasado. Parece que la parte que tiene que ver con los productos, la fabricación, planificación y control ya la tienen más o menos definida.
Clara, que tiene experiencia en la empresa de carpintería y mueble, señala que también deben definir todo lo relacionado con la prevención de riesgos laborales, puesto que está íntimamente ligado al proceso de fabricación, y habrá que elaborar un plan de prevención y estipular las normas de orden y limpieza en la empresa del tío de su amiga.
En primer lugar debes conocer a qué se denomina “riesgo laboral”:
Riesgo laboral es todo aquel aspecto del trabajo que tiene la potencialidad de causar daño.
La prevención de riesgos laborales (PRL) es la disciplina que busca promover la seguridad y salud de los trabajadores mediante la identificación, evaluación y control de los peligros y riesgos asociados a un proceso productivo, además de fomentar el desarrollo de actividades y medidas necesarias para prevenir los riesgos derivados del trabajo.
En España existe legislación que regula todo lo relacionado con la prevención de los riesgos laborales, es la Ley 31/1995, de 8 de Noviembre, prevención de riesgos laborales.
Para saber más
Si te interesa saber más sobre la legislación relativa a seguridad y salud en España, en el siguiente enlace puedes acceder al texto completo de la Ley 31/1995, de 8 de noviembre, de Prevención de Riesgos Laborales.
En la exposición de motivos de la ley, puedes encontrar los siguientes argumentos:
- La protección del trabajador frente a los riesgos laborales exige una actuación en la empresa que desborda el mero cumplimiento formal de deberes y obligaciones empresariales y, más aún, la simple corrección a posteriores situaciones de riesgo ya manifestadas.
- La planificación de la prevención desde el momento mismo del diseño del proyecto empresarial, la inicial evaluación de los riesgos laborales y su actuación periódica a medida que se alteren las circunstancias, la ordenación de un conjunto coherente y globalizador de medidas de acción preventiva adecuadas a la naturaleza de los riesgos detectados y el control de la efectividad de dichas medidas constituyen los elementos básicos del nuevo enfoque en la prevención de riesgos laborales.
- Y, junto a ello, se completa con la información y la formación de los trabajadores dirigidas a un menor conocimiento tanto del alcance real de los riesgos derivados del trabajo como de la forma de prevenirlos y evitarlos, de manera adaptada a las peculiaridades de cada centro de trabajo, a las características de las personas que en él desarrollan su prestación laboral y a la actividad concreta que realizan.
Recuerda que las industrias de carpintería y mobiliario utilizan un tipo de máquinas que pueden resultar muy peligrosas si no se utilizan adecuadamente y con los dispositivos de seguridad necesarios.
Autoevaluación
Solución
6.1.- Normas de orden y limpieza (I).
En la industria de carpintería y mobiliario, para conseguir un grado de seguridad aceptable, tiene especial importancia asegurar y mantener el orden y la limpieza. Son numerosos los accidentes que se producen por golpes y caídas consecuencia de un ambiente desordenado o sucio, suelos resbaladizos (el serrín es un material muy resbaladizo), materiales colocados fuera de su lugar y acumulación de material sobrante o de desperdicio. Todo esto puede constituir, cuando se trata de productos combustibles o inflamables, un factor importante de riesgo de incendio que ponga en peligro los bienes patrimoniales de la empresa e incluso poner en peligro la vida de los ocupantes si los materiales dificultan y obstruyen las vías de evacuación.
El R.D. 486/1997 por el que se establecen las disposiciones mínimas de seguridad y salud en los lugares de trabajo, en su Anexo II regula la obligatoriedad de mantener los locales de trabajo limpios y ordenados, con las siguientes premisas:
- Las zonas de paso, salidas y vías de circulación de los lugares de trabajo y, en especial, las salidas y vías de circulación previstas para la evacuación en casos de emergencia, deberán permanecer libres de obstáculos de forma que sea posible utilizarlas sin dificultades en todo momento.
- Los lugares de trabajo, incluidos los locales de servicio, y sus respectivos equipos e instalaciones, se limpiarán periódicamente y siempre que sea necesario para mantenerlos en todo momento en condiciones higiénicas adecuadas. Con tal fin, las características de los suelos, techos y paredes serán tales que permitan dicha limpieza y mantenimiento. Se eliminarán con rapidez los desperdicios, las manchas de grasa, los residuos de sustancias peligrosas y demás productos residuales que puedan originar accidentes o contaminar el ambiente de trabajo.
- Las operaciones de limpieza no deberán constituir por sí mismas una fuente de riesgo para los trabajadores que las efectúen o para terceros, realizándose a tal fin en los momentos, de la forma y con los medios más adecuados.
Las actuaciones a realizar para la consecución de los objetivos de mantener una empresa “ordenada y limpia” se estructuran en distintas etapas: eliminar lo innecesario y clasificar lo útil; acondicionar los medios para guardar y localizar el material fácilmente; evitar ensuciar y limpiar enseguida; crear y consolidar hábitos de trabajo encaminados a favorecer el orden y limpieza.
Eliminar lo innecesario y clasificar lo útil.
Al principio será difícil distinguir entre lo que es necesario y lo que no lo es. Debes seleccionar y discriminar los elementos en función de su utilidad para realizar el trabajo previsto, disponiendo de contenedores o espacios especiales para la recogida de lo innecesario. El paso siguiente es clasificar lo útil según su grado de necesidad, para esto debes tener en cuenta:
- La frecuencia con que necesitas el elemento. Ello permitirá almacenar fuera del área de trabajo aquello que se utilice esporádicamente.
- La cantidad de elemento necesaria para el trabajo. Para retirar del entorno de trabajo y almacenar fuera del área de trabajo el exceso o sobrante de material.
Acondicionar los medios para guardar y localizar el material fácilmente.
Una vez que has conseguido eliminar lo superfluo e innecesario, el paso siguiente es “ordenar lo útil”. Debe establecerse claramente donde tiene que estar cada cosa de modo que todo trabajador que vaya a necesitarla sepa de manera indudable dónde va a encontrarla y dónde debe devolverla.
La falta de orden en el espacio de trabajo generan una serie de problemas como la pérdida de productividad (pérdidas de tiempo en búsquedas de elementos y en movimientos para localizarlos) y en un incremento de la inseguridad (golpes y contusiones con objetos depositados en cualquier parte).
Recomendación
En los siguientes enlaces puedes ver el RD 486/98 y la Guía Técnica de lugares de trabajo del INSST (Instituto Nacional de Seguridad y Salud Laboral).
Citas para pensar
Cada cosa en su sitio y un sitio para cada cosa.Jim Durkel
6.1.1.- Normas de orden y limpieza (II).
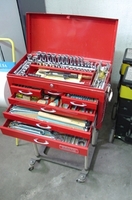
Decisión de las localizaciones más apropiadas.
Para una correcta elección de la localización más apropiada de los distintos elementos de trabajo, tendrás en cuenta aspectos como la frecuencia y la secuencia de uso de los mismos, lo que evitará movimientos y/o desplazamientos innecesarios.
Los principios a aplicar para encontrar las mejores localizaciones para plantillas, herramientas y útiles, debe considerar:
- Su frecuencia de uso, colocando cerca del lugar de uso lo elementos más usados y, más alejados del lugar de uso, los de uso infrecuente u ocasional.
- Almacenar juntos los elementos que se usan juntos y, en su caso, depositados en la secuencia con la que se usan.
- Diseñar un mecanismo de almacenaje del tipo “soltar con vuelta a posición” para herramientas que se usan de modo repetitivo, por ejemplo en una cadena de montaje.
- Los lugares de almacenamiento de herramientas deben ser mayores que éstas de modo que sea fácil y cómodo retirarlas y colocarlas.
- Almacenar las herramientas de acuerdo con su función (almacenar juntas aquellas que sirven para funciones similares) y producto (almacenar juntas aquellas que se usan en el mismo producto).
- Utilizar soportes para el almacenamiento en los que se hayan dibujado los contornos de útiles y herramientas que faciliten su identificación y localización.
Evitar ensuciar y limpiar enseguida.
Las industrias de la madera, por su propio trabajo, crean una capa de polvo sobre máquinas y herramientas que puede en ciertos momentos crear peligro o dificultar su identificación.
La limpieza no debe considerarse como una tarea ocasional que tradicionalmente se ejecuta en verano, a fin de año o cuando se produce un paro de proceso. Determinadas fechas son idóneas para ejecutar tareas especiales de limpieza o para realizar una “limpieza a fondo”. Pero la limpieza no debe realizarse sólo en esas ocasiones, debe ser un hábito diario de trabajo y estar integrada en las tareas diarias de mantenimiento.
El procedimiento de planificación de la limpieza debe estructurarse de manera que contenga:
-
- Un alcance definido, que afectará a todas las unidades funcionales de la empresa.
- Unos destinatarios, que serán los trabajadores de la empresa, cada uno tiene la responsabilidad de mantener limpio y ordenado su entorno de trabajo.
- Unos medios materiales necesarios y puestos a disposición de los trabajadores o ubicados en lugares estratégicos a fin de facilitar las tareas encomendadas.
- Unos métodos de limpieza encaminados a garantizar que las operaciones de limpieza nunca generen peligros ni para el operario que la realiza ni para terceros.
Crear y consolidar hábitos de trabajo encaminados a favorecer el orden y la limpieza.
Si la disciplina de trabajo no se mantiene y los hábitos correctos de trabajo no se consolidan, las condiciones vuelven a los niveles de partida. Para convertir en hábitos la organización, el orden y la limpieza e implantar una disciplina de trabajo es necesario:
- El apoyo firme de una dirección visiblemente involucrada.
- La asignación clara de las tareas a realizar y de los involucrados en la ejecución de las mismas.
- Integrar en las actividades regulares de trabajo las tareas de organización, orden y limpieza, de modo que sean consideradas como “tareas ordinarias”.
- Responsabilizar a una persona del cumplimiento de los procedimientos establecidos sin admitir incumplimientos.
6.2.- Plan de prevención.
Un plan de prevención de riesgos laborales es un documento que, debidamente autorizado, establece y formaliza la política de prevención de una empresa, recoge la normativa, la reglamentación y los procedimientos operativos, definiendo los objetivos de la prevención y la asignación de responsabilidades y funciones a los distintos niveles jerárquicos de la empresa en lo que se refiere a la prevención de riesgos laborales.

El plan constituye una recopilación estructurada de las normas, criterios, procedimientos, instrucciones, acciones y recomendaciones con el fin de asegurar la buena gestión del conjunto de factores que influyen en la prevención de riesgos laborales y en la coordinación con el resto de actividades de la empresa, teniendo en cuenta los objetivos fijados por la dirección.
Como instrumento de gestión, el plan de prevención sirve para asegurar que los efectos de las actividades de la empresa sean coherentes con la política de prevención, definida en forma de objetos y metas.
¿Qué contiene el plan de prevención? Debe contener, como mínimo, lo siguiente:
- La estructura organizativa, las responsabilidades, las prácticas, los procedimientos, los procesos y los recursos necesarios para llevar a cabo la política de prevención de la empresa.
- La documentación necesaria, en forma de procedimientos (pautas a seguir en distintas situaciones) e instrucciones aplicables.
- La implantación de dichos procedimientos e instrucciones en la empresa, teniendo en cuenta la existencia de las normas existentes y de obligado cumplimiento.
Ventajas del plan de prevención.
Las ventajas que proporciona un plan de prevención de riesgos laborales, en el ámbito de la empresa son múltiples y variadas, destacando entre otras, las siguientes:
- Ayudar a conseguir una cultura común en prevención, entre las diferentes áreas y niveles de la empresa, asegurando la correcta comunicación entre las distintas partes interesadas.
- Proporciona a la empresa procedimientos para poner en práctica las metas y objetivos vinculados a su política de prevención, y también para comprobar y evaluar el grado de cumplimiento en la práctica.
- Ayuda a la empresa en el cumplimiento de los requisitos legales y normativos relativos a la ley de prevención de riesgos laborales.
- Demuestra a las partes interesadas la aptitud del plan para controlar los efectos de sus actividades, productos o servicios de la empresa.
- Ofrece las directrices para evaluar y poner en práctica estrategias de gestión relacionadas con la prevención de riesgos laborales.
- Permite introducir mejoras continuas en el sistema, que aumenten y garanticen la calidad de vida laboral.
Autoevaluación
Solución
6.2.1.- Riesgos y medidas de prevención (I).
Riesgos relacionados con locales y equipos de trabajo.
- Cortes y amputaciones por los elementos cortantes de máquinas y herramientas.
Acciones preventivas para mejorar la seguridad:
- Comprar máquinas y herramientas seguras, con el marcado CE.
- Proteger la parte cortante de las máquinas y herramientas con resguardos móviles o móviles con resguardo con enclavamiento, resguardos regulables.
- Utilizar dispositivos de protección que obliguen a la acción simultánea de las dos manos. Mandos sensitivos a dos manos, que obliguen al trabajador a mantener las dos manos sobre los mandos.
- Utilizar resguardos fijos, envolventes o distanciadores, si no es necesario acceder a la zona peligrosa de la máquina.
- Comprobar la eficacia de los dispositivos de protección y de los circuitos de mando.
- Utilizar las máquinas sólo por personas designadas por el empresario, que han de ser informadas de los peligros y adiestradas en su manejo.
- Utilizar las máquinas según las instrucciones del fabricante y sólo en aquellos trabajos para los que han sido diseñadas.
- Prohibir los trabajos a menores en sierras, prensas, tupís y cualesquiera otras máquinas peligrosas.
- Usar los equipos de protección individual que sean necesarios en cada operación (guantes, gafas).
- Golpes por movimientos incontrolados de elementos de máquinas o materiales.
Acciones preventivas para mejorar la seguridad:
- Mantener y respetar las distancias adecuadas entre las máquinas. Los elementos o partes desplazables de las máquinas no deben invadir nunca las zonas de paso.
- Señalizar en el suelo la zona que puede ser invadida por elementos o partes desplazables de las máquinas, especialmente si hay en su proximidad zonas de paso de personas.
- Sujetar o anclar firmemente las estanterías o paredes o suelos y colocar los objetos más pesados en la posición más baja de las estanterías.
- No permitir que se supere la capacidad de la carga de las estanterías.
- Garantizar la estabilidad de los apilamientos, respetando la altura máxima permitida según los casos.
- Instalar barandillas con balaustres o listón intermedio horizontal y rodapiés para impedir la caída de objetos almacenados en altillos, pisos elevados.
- Proyección o desprendimiento de virutas o partículas de madera.
Acciones preventivas para mejorar la seguridad:
- Instalar sistemas de captación y aspiración en las máquinas y herramientas de virutas o partículas de madera.
- Utilizar gafas protectoras contra la proyección de virutas y polvo de madera (serrín).
- Caídas de altura.
Acciones preventivas para la mejora de la seguridad:
- Asegurar todos los elementos de las escaleras de mano, colocar apoyos antideslizantes y prestar atención al ángulo de colocación y forma de utilización.
- Colocar en los altillos o zonas de trabajo elevadas barandillas, barras intermedias y plintos.
- Bloquear el acceso a zonas de trabajo elevadas que carecen de protección en su entorno (bordes de desnivel superior a 2 metros).
- Cubrir las aberturas en el suelo o colocar barandillas, barras intermedias y plintos en todo el perímetro de los huecos.
- Acceso a zonas de almacenamiento elevadas fijas o móviles perfectamente aseguradas, plataformas de trabajo adecuadas o ascensores.
- Caídas en el mismo nivel.
Acciones preventivas para mejorar la seguridad.
- Eliminar la suciedad, y obstáculos contra los que se pueda tropezar.
- Retirar los objetos innecesarios, envases, herramientas que no se están utilizando.
- Ordenas las herramientas y materiales de trabajo en paneles o cajas.
- Marcar y señalar los obstáculos que no puedan ser eliminados.
- Mantener las vías de acceso y los pasos perfectamente iluminados.
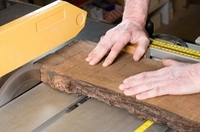
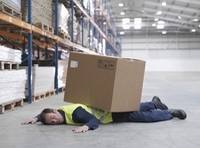
6.2.1.1.- Riesgos y medidas de prevención (II).
Riesgos relacionados con la electricidad.
- Contacto eléctrico.
Acciones preventivas para mejorar la seguridad:
- Antes de comenzar a trabajar, realizar un control visual para detectar defectos reconocibles.
- Puesta a tierra de las masas en combinación con interruptores diferenciales de sensibilidad adecuada.
- Alejamiento y aislamiento de las partes activas de la instalación.
- Llevar a cabo un examen periódico de las instalaciones eléctricas y del material eléctrico por personal especializado.
- No utilizar, hasta que las revise un especialista, maquinaria o herramientas eléctricas que han sufrido un golpe fuerte o han sido afectadas por la humedad.
- En caso de avería, desconectar la tensión, comunicar los daños y hacerlos reparar por personal autorizado para trabajos eléctricos.
Riesgos relacionados con los agentes físicos.
-
Acciones preventivas para mejorar la seguridad:
- Comprar máquinas y equipos de trabajo teniendo en cuenta el nivel de ruido que producen.
- Efectuar revestimientos en paredes y techo, que absorban el ruido.
- Reducir los tiempos de exposición con turnos de trabajo, evitar el paso por zonas de alta exposición.
- Delimitar y señalizar las zonas de exposición al ruido.
- Instalar los ventiladores, extractores, lo más alejados posible de las zonas habituales de trabajo.
- Utilizar medios de protección individual contra el ruido.
- Informar a los trabajadores del riesgo al que están expuestos.
Riesgos relacionados con las sustancias químicas.
- Contacto con productos que contienen sustancias químicas.
Acciones preventivas para mejorar la seguridad:
- Utilizar sustancias con las mismas propiedades pero que sean menos peligrosas.
- Exigir al fabricante las fichas de datos de seguridad de los productos.
- Establecer un plan de acción para la utilización de los productos.
- Evitar el contacto de sustancias con la piel.
- Preparar las mezclas según las instrucciones del fabricante.
- Utilizar los equipos de protección individual según sus prescripciones de uso y la ficha de datos de seguridad de los productos.
- Evitar la respiración de vapores orgánicos nocivos.
- Instalar sistemas de extracción localizada en el lugar de origen de polvos (zona de lijado), vapores (zona de barnizado), humos, nieblas y partículas en suspensión.
- Tener buena ventilación natural en los locales.
- Utilizar equipos respiratorios de protección individual.
Riesgos relacionados con incendios y explosiones.
-
Acciones preventivas para mejorar la seguridad:
- Disponer sólo de la cantidad necesaria de materiales inflamables o combustibles para el trabajo del día, el resto estará en almacén.
- Almacenar los productos inflamables en locales distintos e independientes de los de trabajo, aislados y ventilados, o en armarios completamente aislados.
- Realizar el envasado, desembalaje y mezcla de los productos peligrosos fuera de los almacenes y con las debidas precauciones y el equipo adecuado para cada caso.
- Colocación de extracción de gases localizada y canalizada por conducciones herméticas.
- Colocar extintores de incendios adecuados a la clase de fuego.
- Revisar y mantener las instalaciones eléctricas aisladas y protegidas.
- Señalizar y dejar libres las salidas de emergencia.
- Realizar periódicamente ejercicios de evacuación simulada.
6.2.1.2.- Riesgos y medidas de prevención (III).
Riesgos relacionados con incendios y explosiones.
- Riesgo de explosión.
Acciones preventivas para mejorar la seguridad:
- Revisión anual de la instalación de aire comprimido por el servicio de mantenimiento acreditado.
- Realizar pruebas de presión hidrostática en la instalación de aire comprimido cada 10 años.
- Instalación de extracción localizada canalizada por conducciones herméticas.
- Llevar un control de la concentración de polvos, gases y vapores inflamables.
- Tener especial cuidado con los ciclones donde se almacenan grandes cantidades de polvo de madera y aire sometidos a calentamientos y fricciones.
- Evitar la electricidad electrostática poniendo a tierra sus elementos y manteniendo una humedad relativa alta.
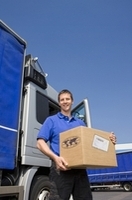
Riesgos relacionados con el diseño de los puestos de trabajo.
- Trabajos realizados manejando cargas o en posiciones forzadas.
Acciones preventivas para mejorar la seguridad:
- Para el transporte de cargas, utilizar medios de transporte o equipos de elevación auxiliares.
- Respetar las cargas máximas según sexo y edad.
- Cargar o transportar pesos pegándolos al cuerpo y en posición erguida.
- Alzar y transportar cargas con ayuda de otras personas.
- Disminuir el peso de las cargas.
- Posibilitar los cambios de posturas.
- Colocar los útiles y demás medios de trabajo al alcance de la mano.
- Condiciones medioambientales del local de trabajo.
Acciones preventivas para mejorar la seguridad:
- Proporcionar ropa de protección adecuada.
- Hacer pausas durante los trabajos pesados cuando el cuerpo está sometido a la influencia del calor.
- Regular la temperatura de acuerdo a las exigencias.
- Aislar del calor y la humedad.
- Humedecer el aire del local.
- Evitar corrientes de aire.
- Instalar, en su caso, sistemas de ventilación forzada.
- Iluminación del lugar de trabajo.
En función del tipo de trabajo necesitarás una intensidad diferente de luz.
Acciones preventivas para mejorar la seguridad:- Medir la intensidad de iluminación en cada puesto antes de trabajar.
- Corregir los lugares oscuros.
- Eliminar o apantallar las fuentes de luz deslumbrantes.
- Limpiar periódicamente las lámparas y luminarias.
Riesgos relacionados con la organización del trabajo.
- Situaciones de trabajo que producen estrés.
Acciones preventivas para mejorar la seguridad:
- No prolongar la jornada habitual de trabajo y compensarla preferentemente con descanso adicional.
- Respetar los descansos.
- Planificar los diferentes trabajos de la jornada laboral teniendo en cuenta una parte de imprevistos.
- Seleccionar al trabajador según la actividad que ha de desarrollar.
- Estado de utilización de los Equipos de Protección Individual (EPI).
Acciones preventivas para la mejora de la seguridad:
- Elegir EPI's correctos y en número suficiente.
- Revisar periódicamente el estado y el funcionamiento de los EPI`s.
- Cambiar los equipos defectuosos o caducados.
- Señalar los daños por el uso incorrecto de los EPI.
- Realizar instrucciones periódicas sobre el uso y mantenimiento de los EPI.
6.2.2.- Medidas preventivas en el uso de herramientas y materiales de carpintería.
Prácticamente todas las máquinas que se utilizan en la industria de la madera, disponen de herramientas de corte con alto grado de afilado que giran a un elevado número de revoluciones. El trabajo en alguna de ellas hace que las manos del operario se mantengan cerca de las herramientas de corte. Muchos dispositivos de seguridad son retirados o mal ajustados por los propios operarios buscando rapidez en la preparación o ganancia de tiempo. Esto implica un riesgo muy grave que se materializa habitualmente en amputaciones.
A este riesgo principal se le añaden los propios que se dan en los pequeños talleres, como desorden, falta de limpieza, apilamientos incorrectos, manipulación manual de cargas, electrocuciones, incendios, explosiones.
Por todo esto es necesario vigilar continuamente la correcta colocación de los resguardos de protección así como de los sistemas de ventilación general y localizada. El uso de equipos de protección así como de las medidas de protección de la maquinaria. El uso de equipos de protección individual complementará las acciones de protección colectiva. Y una formación continua ayudará a conseguir un lugar de trabajo más seguro.
A continuación tienes una serie de medidas preventivas a tener en cuenta en el uso de herramientas de carpintería:
Sierras y serruchos:
- Sujetar correctamente el elemento a serrar.
- Coger firmemente con una mano el serrucho o sierra y con la otra el objeto a serrar.
Lijadoras:
- Sujetar fuertemente las herramientas mientras se utilizan.
- Cerciorarse de que no existe elemento en el banco de trabajo que pueda obstruir la herramienta.
- Si la herramienta se atasca, desenchufarla antes de desatascarla.
Formones y rascadores:
- Comprobar que la parte cortante de la herramienta esté muy afilada.
- Sujetar firmemente el material a trabajar.
- Al manipular el formón, evitar dirigirlo hacia los miembros o partes del cuerpo.
Tenazas:
- Utilizarlas sólo para quitar clavos y alambres o piezas metálicas de sección y resistencia media.
- No utilizarlas para sujetar piezas sometidas a esfuerzos.
- Entre los brazos de las tenazas debe existir espacio suficiente para evitar el aprisionamiento de la mano del operario.
Destornilladores:
- Elegir el adecuado al tamaño del tornillo.
- Comprobar que la herramienta está en buen estado.
- La mano libre no ha de quedar nunca en la trayectoria del destornillador.
- No apoyar la pieza en la mano, sino en lugar firme.
- No utilizarlo como palanca, cincel, punzón.
Sierra eléctrica (caladora o circular):
- Eliminar las partículas que se sitúen delante de la cuchilla.
- Al realizar el trabajo, sujetar fuertemente la sierra.
- Mantener una distancia prudencial de seguridad con la sierra.
- Si la sierra se atasca, desenchufarla e intentar desatascarla.
Taladro (portátil o de banco):
- Utilizar la broca adecuada al trabajo a realizar.
- Agarrar fuertemente el brazo del taladro mientras se esté utilizando.
- Utilizar la llave para cambiar la broca. No hacerlo manualmente.
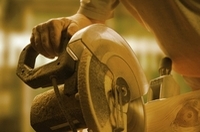

Recomendación
En el siguiente enlace puedes ver la normativa relacionada con los equipos de trabajo:
Autoevaluación
Solución
7.- Gestión de la protección ambiental.
Caso práctico
Entre los tres han elaborado un plan de prevención de riesgos, que debido a la actividad de la empresa consideran muy importante.
Clara les propone, además, elaborar el plan de gestión ambiental y, aunque les produce extrañeza, Clara les explica que últimamente se está tomando conciencia de la importancia del respeto al medio ambiente, por lo que es obligatorio cumplir la normativa establecida respecto a la gestión de residuos.
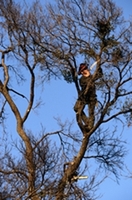
En las industrias de carpintería y mobiliario se realizan una serie de tareas consistentes en confeccionar e interpretar planos de construcción de muebles, presupuestar, elaborar, montar y reparar puertas y ventanas, el revestimiento de paredes, escaleras y armarios. Estas tareas se pueden realizar en taller o a pie de obra. Todo ello conociendo y aplicando la legislación vigente.
En la actividad se utiliza recursos valiosos como madera y energía eléctrica se maneja maquinaria cuyo funcionamiento requiere de sustancias peligrosas (aceites y grasas), se emplean algunos productos potencialmente peligrosos como las colas y se produce la emisión de ruido y polvo.
Debes sensibilizarte sobre la afección que se genera al medio ambiente, aportando soluciones mediante el conocimiento de la actividad y la propuesta de prácticas ambientales correctas.
Para saber más
Si eres una persona respetuosa con el medio ambiente y tienes interés en conocer la normativa española y europea referente a este tema, en el siguiente enlace podrás encontrar más información.
Para elaborar un plan medioambiental efectivo primero debes conocer los recursos que se utilizan en carpintería:
- Instalaciones: acometida eléctrica, almacén, toma de agua.
- Equipo y maquinaria: compresor, cepilladora, regruesadora, sierras de distintos tipos, taladros, fresadora, ingletadora, lijadora.
- Herramientas y utillaje: plantillas, martillos, sierras, nivel, escuadra, plomadas, destornilladores, fresas, cuchillas, brocas, útiles de dibujo, metros.
- Material de consumo: madera, tableros de diversos tipos, cola, masilla, barnices, tornillos, herrajes, cristales, clavijas, disolventes.
- Agua.
- Energía.
- Combustible.
Autoevaluación
Solución
7.1.- Aspectos e impactos ambientales a considerar.
En las tareas relacionadas con la carpintería y mobiliario se generan una serie de residuos:
- Residuos asimilables a urbanos: papel, cartón, envases (plástico, vidrio, metal), restos de comida, trapos y ropa, herramientas viejas.
- Residuos industriales no peligrosos: serrín, plásticos, vidrios.
- Residuos peligrosos: restos de barnices, disolventes, colas, baterías, trapos y materiales impregnados de productos químicos, productos químicos caducados, fluorescentes, aerosoles, productos tóxicos y sus envases, pilas.
- Vertidos líquidos: aguas procedentes de la limpieza de maquinaria y herramientas.
- Emisiones a la atmósfera.
En el desarrollo de la actividad industrial de carpintería y mobiliario se contribuye a distintos problemas ambientales, debiendo prestar especial atención y no incurrir en los puntos que se indica:
- Agotamiento de recursos:
- No usando productos certificados por el Consejo de Administración Forestal.
- No almacenando correctamente la madera, favoreciendo la aparición de deformaciones en la misma y provocando que no pueda utilizarse.
- No optimizando el despiece y el corte.
- No controlando que los disolventes se contaminen con disoluciones acuosas u otros disolventes.
- No adquiriendo maquinaria y herramientas duraderas o susceptibles de ser reparadas.
- No controlando el consumo de agua y energía.
- Contaminación atmosférica:
- Empleando electricidad procedente de centrales de combustión de carbón o gas natural.
- No contratando proveedores madereros cercanos.
- Manteniendo la maquinaria en funcionamiento cuando no se está utilizando.
- Reducción de la capa de ozono:
- Utilizando extintores con halón. En la actualidad está prohibida su fabricación por tratarse de un producto responsable del deterioro de la capa de ozono, si bien todavía quedan en uso extintores portátiles a base de halón, para sustituirlos están apareciendo nuevos productos que no son dañinos ecológicamente, denominados halotrones o halocleanes.
- Empleando aerosoles y sistemas de refrigeración con CFC.
- Contaminación del agua:
- Evacuando en los desagües los restos de aguas de lavados de maquinaria e instalaciones.
- No evitando derrames de aceites y combustibles que al ser limpiados con agua acabarán en los desagües.
- No empleando limpiadores respetuosos con el medio ambiente.
- Residuos:
- No separando los residuos.
- Comprando colas con componentes peligrosos.
- Adquiriendo productos con envases innecesarios o no retornables.
- Adquiriendo maderas tratadas con compuestos tóxicos.
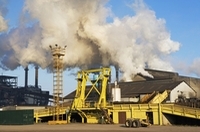
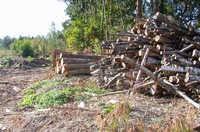
7.2.- Buenas prácticas ambientales en aprovisionamiento de recursos.
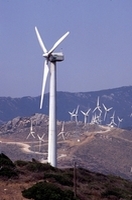
Con respecto a la generación de residuos debes seguir las siguientes pautas:
- Minimizar la producción de residuos y emisiones.
- Correcta gestión de los residuos generados, evitando el daño ambiental.
- Cumplir la normativa vigente para la actividad y disponer de todos los permisos y licencias necesarios para desarrollar la actividad.
- Fomentar el ahorro de materiales, agua y energía.
- Emplear materiales con certificaciones que acrediten una gestión ambiental adecuada.
- Tratar de elegir aquellos productos que provengan de recursos renovables, fabricados con el mínimo impacto ambiental y consumo de energía y con materiales reciclados.
- Conservar técnicas y labores tradicionales y locales.
En la industria maderera se utilizan gran variedad de recursos, materiales, maquinaria, equipos, utensilios. A continuación verás unos consejos para su aprovisionamiento, almacenamiento, uso y mantenimiento, respetuoso con el medio ambiente.
Aprovisionamiento de recursos.
- Maquinaria, equipos y utensilios:
- Adquirir equipos y maquinaria que tengan los efectos menos negativos para el medio.
- Emplear herramientas y útiles más duraderos y fácilmente reparables, y aquellos que requieran menor gasto, consumo de energía y recursos en su elaboración.
- Utilizando extintores sin halones.
Materiales:
- Conocer el significado de los símbolos o marcas ecológicos.
- Intentar utilizar materiales y productos ecológicos con certificados de que el impacto ambiental durante su ciclo de vida es el menor posible.
- Evitar los materiales tóxicos y peligrosos.
- Adquirir madera procedente de explotaciones sostenibles y certificadas por el Consejo de Administración Forestal.
- Tratar de adquirir envases fabricados con materiales reciclados, biodegradables y retornables.
- Evitar el exceso de envoltorios y embalajes en las compras.
- Productos químicos:
- Conocer los símbolos de peligrosidad y toxicidad.
- Comprobar la correcta etiquetación de los productos y que las instrucciones de manejo sean claras.
- Elegir aquellos productos de limpieza que siendo eficaces sean respetuosos con el medio ambiente.
- Para tratar la madera, elegir alternativas a los protectores químicos, como pueden ser las sales de boro hidrosolubles.
Autoevaluación
Solución
7.3.- Buenas prácticas ambientales en almacenamiento, uso y mantenimiento de recursos.
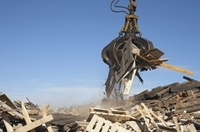
Almacenamiento de recursos.
- Almacenar los elementos de manera que puedan ser identificados correctamente.
- Cumplir las normas de almacenamiento de los materiales, cerrando y etiquetando los recipientes que contengan productos peligrosos.
- Colocar maderas y tableros de manera que se evite su deformación.
- Correcta manipulación de productos peligrosos para evitar riesgos, y aislarlos del resto.
- Controlar la caducidad de los materiales.
Uso de recursos.
- Materiales y maquinaria:
- Reducir los residuos empleando la maquinaria y herramientas adecuadas en función del trabajo que se desarrolle.
- Tener la maquinaria en funcionamiento sólo el tiempo imprescindible para evitar la contaminación sonora y atmosférica.
- Instalar sistemas de recogida eficaces que reduzcan la emisión de polvo.
- Reutilizar materiales, componentes y envases, si es posible.
- Separar los residuos. Teniendo especial cuidado en separar maderas sin productos de acabado de maderas con productos, como ceras, barnices.
- Productos químicos:
- Utilizar los productos químicos siguiendo la dosificación recomendada por el fabricante y buscar aquellos productos más respetuosos con el medio.
- Vaciar completamente los envases de estos productos para reducir los residuos.
- Gestionar correctamente los residuos procedentes de la limpieza de equipos, herramientas e instalaciones (minimizando o reutilizando).
Debes conocer
Es importante que conozcas la simbología utilizada para señalizar los productos peligrosos, a continuación tienes una presentación que te los muestra.
- Energía:
- Ahorrar energía mientras se trabaja; aprovechar al máximo la iluminación natural, colocar temporizadores y lámparas de bajo consumo y larga duración.
- Promover opciones que reduzcan el consumo energético.
Mantenimiento de recurso.
- Limpiar las lámparas para optimizar la iluminación.
- Realizar un mantenimiento preventivo de los equipos para optimizar el consumo de energía y agua.
- Inspeccionar la acometida de agua para evitar fugas y averías.
Autoevaluación
Solución
7.4.- Gestión de residuos (I).
Otro punto importante dentro de la gestión de protección medioambiental es la gestión de residuos. Debes conocer cómo tratar cada tipo de residuo y dónde se debe depositar.
Se mejora y contribuye a una buena gestión ambiental de los residuos en general:
- Utilizando tableros que contengan materiales reciclados.
- Utilizando elementos cuyos desechos posean una elevada aptitud para ser reciclados.
- Gestionando desechos como restos de madera y tableros, viruta y serrín a través de bolsas de subproductos.
- Rechazando los materiales que se transforman en residuos tóxicos o peligrosos al final de su uso como los elementos organoclorados (PVC, CFC).
Con un manejo de los residuos que evite daños ambientales y a la salud de las personas, y para ello:
- Informándose de las características de los residuos y de los requisitos para su correcta gestión.
- Cumpliendo la normativa, lo que supone:
- Separar correctamente los residuos.
- Presentar por separado o en recipientes especiales los residuos susceptibles de distintos aprovechamientos o que sean objeto de recogidas específicas.
- Depositar los residuos en los contenedores determinados para ello.
- Seguir las pautas establecidas en el caso de residuos objeto de servicios de recogida especial.
A continuación verás cómo gestionar los residuos según su tipología:
Residuos asimilables a urbanos.
Han de depositarse en los contenedores habilitados para ello y siguiendo la normativa vigente, ya que son residuos que se recogen a domicilio.
Residuos industriales no peligrosos.
- En las instalaciones se han debido separar y depositar cada tipo de residuo en contenedores en función de las posibilidades de recuperación y requisitos de gestión.
- En el traslado al exterior se puede solicitar la recogida y transporte, la autorización para el depósito en el Centro de Tratamiento o entregarlos a gestores autorizados.
Residuos peligrosos.
- En las instalaciones:
- Separar correctamente los residuos.
- Identificar los contenedores mediante etiquetas, que por legislación debe contener:
- Código de residuo.
- Símbolo correspondiente según sea producto nocivo, tóxico.
- Nombre, dirección y teléfono del titular de los residuos.
- Fecha de envasado (cuando se tiene el contenedor completo).
- Almacenar los residuos en contenedores adecuados y que no se vean afectados por los materiales que contienen, además de ser resistentes a la manipulación.
- Colocar los residuos en zonas bien ventiladas, a cubierto del sol y la lluvia, separados de focos de calor o llamas, que no puedan reaccionar entre sí y en caso de que ocurriera un accidente que sus consecuencias fueran mínimas.
- Dar de alta los residuos en un registro, con los siguientes datos:
- Origen de los residuos.
- Cantidad, tipo de residuo y código de identificación.
- Fecha de cesión de los residuos (la de entrega a un gestor).
- Fecha de inicio y final del almacenamiento.
- En el traslado al exterior:
- Todos los residuos peligrosos y los envases que los hayan contenido han de ser gestionados por un gestor autorizado.
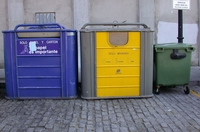
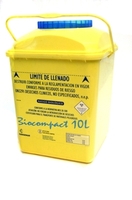
7.4.1.- Gestión de residuos (II).
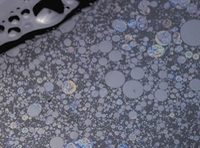
Vertidos líquidos.
- Poseer la autorización de vertido, de la Confederación Hidrográfica si se realiza a un cauce público y del Ayuntamiento o Mancomunidad si se hace a colector.
- En el caso de que los vertidos generados sobrepasen los límites establecidos de contaminantes, se deben efectuar en las instalaciones de la actividad los pretratamientos necesarios para garantizar las limitaciones establecidas.
- Se deben instalar los dispositivos necesarios para toma de muestras y para medir el caudal de vertido.
- Está prohibido verter a la red de colectores públicos:
- Materias que impidan el correcto funcionamiento o el mantenimiento de los colectores.
- Sólidos, líquidos o gases combustibles, inflamables o explosivos y tampoco irritantes, corrosivos o tóxicos.
- Evitar: el vertido de aguas residuales procedente de la limpieza de las instalaciones, maquinaria y herramienta recogiendo y depurando este líquido.
- Reducir vertidos: controlando el agua de limpiezas en determinados procesos, reutilizándola si fuera posible y tratándola antes de verterla a cauce público si no cumple las limitaciones de vertido.
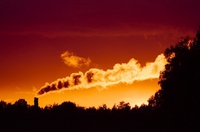
Emisiones atmosféricas.
Cumplir la normativa vigente en la forma en que proceda:
- Comunicarlas a la Administración competente como actividades potencialmente contaminantes.
- En algunas comunidades, disponer de dos libros de registro oficiales suministrados por la Administración:
- Libro de emisiones.
- Libro de mantenimiento.
- En el libro de emisiones se deben registrar los resultados de los controles que es necesario realizar.
- En el libro de mantenimiento deben constar las operaciones de mantenimiento realizadas en las instalaciones.
Reducir las emisiones:
- Polvo: reducir las emisiones empleando sistemas de recogida y extracción eficaces.
- Ruido: reducir estas emisiones empleando maquinaria y utensilios menos ruidosos y manteniendo desconectados los aparatos cuando no se estén utilizando.
Autoevaluación
Solución
Anexo.- Licencias de recursos.
Recurso (1) | Datos del recurso (1) | Recurso (2) | Datos del recurso (2) |
---|---|---|---|
![]() |
Autoría: Stockbyte. Licencia: Uso Educativo no comercial para plataformas de FPaD. Procedencia: CD-DVD Num. V43. |
![]() |
Autoría: Latinstock. Licencia: Uso Educativo no comercial para plataformas de FPaD. Procedencia: Latinstock código: 14083JUI. |
![]() |
Autoría: Latinstock. Licencia: Uso Educativo no comercial para plataformas de FPaD. Procedencia: Latinstock código: 42-25067683. |
![]() |
Autoría: Stockbyte. Licencia: Uso Educativo no comercial para plataformas de FPaD. Procedencia: CD-DVD Num. V07. |
![]() |
Autoría: Photodisc. Licencia: Uso Educativo no comercial para plataformas de FPaD. Procedencia: CD-DVD Num. V43. |
![]() |
Autoría: Latinstock. Licencia: Uso Educativo no comercial para plataformas de FPaD. Procedencia: Latinstock código: 25954. |
![]() |
Autoría: Latinstock. Licencia: Uso Educativo no comercial para plataformas de FPaD. Procedencia: Latinstock código: GWJ2846450. |
![]() |
Autoría: Latinstock. Licencia: Uso Educativo no comercial para plataformas de FPaD. Procedencia: Latinstock código: 42-20846234. |
![]() |
Autoría: Latinstock. Licencia: Uso Educativo no comercial para plataformas de FPaD. Procedencia: Latinstock código: 42-20847728. |
![]() |
Autoría: Latinstock. Licencia: Uso Educativo no comercial para plataformas de FPaD. Procedencia: Latinstock código: 42-26838922. |
![]() |
Autoría: Latinstock. Licencia: Uso Educativo no comercial para plataformas de FPaD. Procedencia: Latinstock código: 20022423. |
![]() |
Autoría: Latinstock. Licencia: Uso Educativo no comercial para plataformas de FPaD. Procedencia: Latinstock código: TI0700840. |
![]() |
Autoría: Latinstock. Licencia: Uso Educativo no comercial para plataformas de FPaD. Procedencia: Latinstock código: 42-15512363. |
![]() |
Autoría: Latinstock. Licencia: Uso Educativo no comercial para plataformas de FPaD. Procedencia: Latinstock código: BLD054506. |
![]() |
Autoría: Latinstock. Licencia: Uso Educativo no comercial para plataformas de FPaD. Procedencia: Latinstock código: 42-23779110. |
![]() |
Autoría: Stockbyte. Licencia: Uso Educativo no comercial para plataformas de FPaD. Procedencia: CD-DVD Num. CD165. |
![]() |
Autoría: Latinstock. Licencia: Uso Educativo no comercial para plataformas de FPaD. Procedencia: Latinstock código: IS472-034. |
![]() |
Autoría: Latinstock. Licencia: Uso Educativo no comercial para plataformas de FPaD. Procedencia: Latinstock código: 42-22936746. |
![]() |
Autoría: Latinstock. Licencia: Uso Educativo no comercial para plataformas de FPaD. Procedencia: Latinstock código: 42-18391514. |
![]() |
Autoría: Latinstock. Licencia: Uso Educativo no comercial para plataformas de FPaD. Procedencia: Latinstock código: 26506. |
![]() |
Autoría: Latinstock. Licencia: Uso Educativo no comercial para plataformas de FPaD. Procedencia: Latinstock código: 42-16309669. |
![]() |
Autoría: Latinstock. Licencia: Uso Educativo no comercial para plataformas de FPaD. Procedencia: Latinstock código: 42-26116586. |
![]() |
Autoría: Stockbyte. Licencia: Uso Educativo no comercial para plataformas de FPaD. Procedencia: CD-DVD Num. V43. |
![]() |
Autoría: Latinstock. Licencia: Uso Educativo no comercial para plataformas de FPaD. Procedencia: Latinstock código: TI0601338. |
![]() |
Autoría: Latinstock. Licencia: Uso Educativo no comercial para plataformas de FPaD. Procedencia: Latinstock código: 18391526. |
![]() |
Autoría: Latinstock. Licencia: Uso Educativo no comercial para plataformas de FPaD. Procedencia: Latinstock código: 42-21780775. |
![]() |
Autoría: Latinstock. Licencia: Uso Educativo no comercial para plataformas de FPaD. Procedencia: Latinstock código: 42-24304137. |