U.T.4.- Control del proceso de fabricación en carpintería y mueble.
U.T.4.- Control del proceso de fabricación en carpintería y mueble.
Caso práctico
Ana y Clara han estado echando una mano al tío Fernando, en la gestión de productos y producción de su fábrica.
Al tío Fernando le han hecho un encargo y Ana y Clara le han realizado los procesos de fabricación de los productos que tiene que ejecutar en las próximas semanas, de esta forma, le ha resultado mucho más fácil acopiar el material necesario. También ha contratado a un alumno de grado medio que estuvo realizando las FCT en la empresa del tío Fernando, y cuyo trabajo dio muy buenos resultados.
Menos mal que Ana y Clara le aconsejaron, de lo contrario él habría contratado al menos a dos personas para que le ayudasen a realizar el trabajo de ese encargo, pero está claro, que bien organizado, se puede ahorrar un poco de cada sitio.
Lanzada la producción que tiene que salir en las próximas dos semanas, parece que por fin todo va bien, pero Fernando, que es muy observador, se da cuenta de que todo ese trabajo se podría optimizar mucho más, como planteamiento inicial estuvo muy bien lo que le propusieron Ana y Clara, pero ya se sabe, cuando se lleva a la realidad lo escrito en el papel siempre hay sorpresas.
Fernando llama a su sobrina Ana para contarle lo que había observado y Ana le comenta a su vez a su tío que es tan importante planificar bien como el control posterior del proceso.

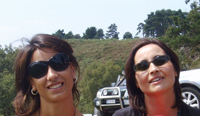
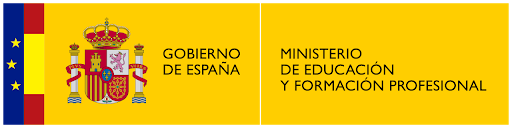
1.- Tiempos.
En primer lugar debes conocer en qué se basa el sistema de tiempos que se irá desarrollando en esta unidad.
Es una técnica utilizada para determinar con la mayor exactitud posible, partiendo de un número de observaciones, el tiempo para llevar a cabo una tarea determinada con arreglo a un rendimiento preestablecido.
Debes compaginar las mejores técnicas y habilidades disponibles a fin de lograr una eficiente relación hombre máquina. Una vez que se establece un método de trabajo, la responsabilidad de determinar el tiempo requerido para fabricar el producto queda dentro del alcance de este trabajo. También está incluida la responsabilidad de vigilar que se cumplan las normas o estándares predeterminados, y de que los trabajadores sean retribuidos adecuadamente según su rendimiento.
Las medidas de mejora de las técnicas incluyen también la definición del problema en relación con el costo esperado, la reparación del trabajo en diversas operaciones, el análisis de cada una de éstas para determinar los procedimientos de manufactura más económicos según la producción considerada, la utilización de los tiempos apropiados y, finalmente, las acciones necesarias para asegurar que el método prescrito sea puesto en operación perfectamente.
Es necesario que, para llevar a cabo un estudio de tiempos, el analista tenga la experiencia y conocimientos necesarios y que comprenda en su totalidad una serie de elementos. A continuación tienes una serie de elementos que describen cómo planificar la realización de una medición de tiempos:
-
Selección de la operación: que operación se va a medir, no es lo mismo medir el tiempo que lleva lijar una puerta lisa que el tiempo que lleva lijar una puerta plafonada. Su tiempo, en primer orden es una decisión que depende del objetivo general que persigues con el estudio de la medición. Se pueden emplear distintos criterios para hacer la elección:
- El orden de las operaciones según se presentan en el proceso.
- La posibilidad de ahorro que se espera en la operación. Relacionado con el costo anual de la operación que se calcula mediante la siguiente ecuación:
- Costo anual de operación = actividad anual x tiempo de operación x salario horario.
-
Según necesidades específicas.
-
Selección del operador: al elegir al trabajador se deben considerar los siguientes puntos: habilidad, deseo de cooperación, temperamento y experiencia.
-
Actitud frente al trabajador:
- El estudio debe hacerse a la vista y conocimiento de todos.
- El analista debe observar todas las políticas de la empresa y cuidar de no criticarlas con el trabajador.
- No debe discutirse con el trabajador ni criticar su trabajo sino pedir su colaboración.
- Es recomendable comunicar al sindicato la realización de estudios de tiempos.
- El operario espera ser tratado como un ser humano y en general responderá favorablemente si se le trata bien y francamente.
Citas para pensar
Escoger el propio tiempo es ganar tiempo. Sir Francis Bacon (1561-1626) Filósofo y estadista británico
1.1.- Estudio de tiempos.
Para la realización de un estudio de métodos de trabajo se precisa una acción paralela de medida de tiempo, que dan la base para la determinación del contenido del trabajo de cada uno de los elementos que componen dicho trabajo.
La medición del trabajo es la aplicación de técnicas para determinar el tiempo que invierte un trabajador cualificado en llevar a cabo una tarea definida efectuándola según una norma de ejecución preestablecida. La importancia de la medida del trabajo no sólo se limita a su necesidad para un adecuado análisis de los métodos de producción, sino que constituye un elemento imprescindible para el adecuado enfoque de muy variados aspectos del proceso productivo en el conjunto de la empresa, tales como:
- Programación de la producción: determinación de plazos de entrega.
- Equilibrado de líneas de producción: dimensionado de equipos.
- Cálculo de costes: formulación de presupuestos.
- Medida de la actuación personal para la determinación de niveles retributivos y cálculo de incentivos.
En la gestión de una empresa no existe ningún ámbito que pueda prescindir de la correcta determinación de tiempos de ejecución de las distintas operaciones que en ella se desarrollan, a través de una adecuada política de medida del trabajo.
En la política de trabajo, la primera decisión a tomar se refiere a la elección de los medios utilizados para realizar la medida, dentro de la gama de posibilidades de la que se dispone actualmente. Esta elección viene determinada por la exactitud y precisión exigidas según la utilización que se haga de los tiempos obtenidos.
En el caso de que los tiempos reales de ejecución de las operaciones se comparen con tiempos normales, calculados previamente para establecer un sistema de incentivo salarial, la exactitud y precisión de las medidas realizadas para la obtención de los tiempos normales debe ser mucho mayor que cuando la medida de tiempos se utiliza sólo para fines organizativos (planificación, costes.).
Una tarea está formada por un conjunto de operaciones. Cada operación tiene un tiempo normal, este tiempo no es la media de una serie de valores que se toman al azar sino es el valor modal de un muestreo de valores tomados de tal manera que el tiempo que sale es el valor que más se repite y por lo tanto, el más normal y el que se asigna.
Para cada operación hay que tomar un número determinado de tiempos en función de su complejidad, dimensión, repetición e importancia. Se debe hacer un escrutinio por cada operación que se realiza en fábrica, ya que para reflejar en un diagrama lo que ocurre en un proceso productivo, hay que ser lo más detallista posible para ser justos y que no se produzca ninguna desviación, con el objeto de que los tiempos sean equitativos tanto para la empresa como para el trabajador; una vez que se terminan de hacer estos escrutinios debes calcular cuál es la frecuencia normal de cada operación, es decir, las veces que se repite. Con todo esto lo que se pretende es llegar a simular en una hoja de cálculo todas las variables y parámetros que influyen en el tiempo de una tarea.
Autoevaluación
1.1.1.- Etapas del estudio de tiempos.
El desarrollo lógico que se debe seguir en el estudio de trabajo está dividido en una serie de etapas o fases que configuran el procedimiento básico de análisis de cualquier proceso de trabajo. Las fases son las siguientes:
- Selección de la tarea: se basa en la elección del trabajo objeto de estudio, teniendo en cuenta aspectos de índole técnica, económica y humana.
- Registro del método actual: consiste en recolectar los datos más relevantes acerca de la tarea seleccionada o métodos de estudio utilizando para ello las técnicas más convenientes, como pueden ser las representaciones gráficas.
- Examen del método actual de trabajo: se basa en la detección de cuantos errores se puedan encontrar en la aplicación del método actual; por ello, en esta fase que emplear al máximo el espíritu crítico y hacerse preguntas del tipo ¿Por qué se hace esto? ¿Por qué lo hace esta persona? ¿Para qué lo hace?
- Desarrollo del nuevo método: en base a la información obtenida anteriormente se estudia la aplicación de una mejor forma (más racional y económica) de llevar a cabo el proceso de trabajo.
- Evaluación de los resultados obtenidos con el nuevo método: se trata de comparar las ventajas del anterior método con las del nuevo método verificando que estas últimas superen a las anteriores para que tenga sentido la implantación del nuevo método.
- Definición del nuevo método y tiempos asociados: en esta fase del estudio del trabajo se persigue la concreción del nuevo método, tanto en forma como en tiempo, presentándolo, verbalmente o por escrito, a todas las personas quienes concierne, pudiendo para ello utilizarse incluso demostraciones reales o figuradas.
- Implantación del nuevo método y formación del personal: en este momento del estudio se implantan las nuevas formas de ejecución del trabajo precisándose para ello un cierto periodo de formación del personal afectado.
- Control y seguimiento del nuevo método: tiene por objeto detectar las posibles desviaciones que puedan surgir con la aplicación del método mejorado, es decir, comparar los resultados obtenidos con los objetivos propuestos.
Antes de iniciar un estudio en un centro de trabajo debes tener en cuenta varias puntualizaciones. En primer lugar debes fijar los límites del estudio y señalar lo que abarcará, si será un estudio de una operación completa o sólo de una parte, si serán objeto de estudio los materiales o las personas. Estas cuestiones especificarán el campo objeto de estudio. En segundo lugar debes priorizar las actividades sobre las que recaerá el análisis sin olvidar la idea básica: el costo de realización del estudio nunca debe superar el beneficio que obtendrás con las mejoras introducidas como consecuencia del estudio.
Existen una serie de recomendaciones básicas orientadas a la realización de estudios técnico-laborales en empresas manufactureras. Destacan las siguientes:
- Para disminuir los ciclos de trabajo se recomienda:
- El empleo de maquinaria moderna, eficaz y segura.
- La realización de un regular y exhaustivo mantenimiento de los útiles de trabajo y de la maquinaria empleada en la actividad.
-
Utilización de materias primas que sean de calidad adecuada y de dimensiones acordes con el producto para evitar desechos.
-
Para reducir los tiempos improductivos:
- Mantener la máquina en perfecto estado de conservación para evitar averías.
- Programar la fabricación con hojas de instrucciones que recojan al detalle los elementos incluidos en el proceso de producción.
- Planificar la fabricación de forma que los lotes de producción resulten adecuados reduciendo al mínimo el número de esperas y la cantidad de material en curso de fabricación.
1.1.2.- Tipos de tareas.
A la hora de realizar un estudio de tiempos te puedes encontrar con distintos tipos de tareas o elementos. Estos elementos de trabajo se pueden clasificar en base a los siguientes criterios principales:
En relación al ciclo de trabajo pueden ser:
- Regulares: son aquellos elementos que aparecen una sola vez en cada ciclo de trabajo; por tanto, su frecuencia de aparición es constante y regular.
- Irregulares: son los que se necesitan para completar un ciclo de trabajo, pero su aparición no es necesaria en todos los ciclos. Es decir, estos elementos se presentan cada cierto número de ciclos o cada cierto número de piezas en el caso de actividades de fabricación; por tanto, su frecuencia de aparición es irregular.
- De frecuencia: estos elementos combinan características de los dos tipos de elementos anteriores, son similares a los elementos irregulares pero tienen una secuencia constante de aparición.
- Extraños: son elementos que no se necesitan para completar el ciclo de trabajo y, por tanto, en la medida de lo posible, deben ser eliminados de él (por ejemplo, la indisposición de un trabajador durante el ciclo).
Los elementos relacionados con el ejecutante pueden ser:
- Manuales sin máquina.
- Manuales con máquina.
- De máquina automática.
- De máquina con avance manual.
Los elementos manuales se realizan con la intervención del operario, y pueden ser sin máquina o también llamados libres, cuya duración depende de la actividad del operario, y con máquina, en los que interviene el trabajo del hombre que alimenta o ayuda a la máquina. Estos últimos se clasifican a su vez en elementos con máquina parada o con máquina en marcha.
Los elementos de máquina son elementos de trabajo realizados propiamente por la máquina. Pueden ser con máquina automática, que no requieren de la intervención del operario, tan sólo pueden requerir o no su vigilancia; o con máquina de avance manual, en los cuales la máquina trabaja con ayuda del operario en determinados momentos.
Autoevaluación
Solución
2.- Método de medición de tiempos.
Caso práctico
Ana y Clara hicieron un buen trabajo aconsejando a su tío.
Para primero le estuvieron haciendo varías preguntas, ya que es él la persona que sabe cuánto se tarda más o menos en realizar cada actividad. Además Ana y Clara no tenían la posibilidad de aplicar otros métodos que existen para la medición de tiempos.
Como verás, las técnicas de organización sirven para calcular el tiempo que necesita un operario cualificado para realizar una tarea determinada siguiendo un método preestablecido.
El conocimiento del tiempo que se necesita para la ejecución de un trabajo es tan necesario en la industria de la madera, como lo es para el hombre en su vida social. De la misma manera, la empresa, para ser productiva, necesita conocer los tiempos que permitan resolver problemas relacionados con los procesos de fabricación en relación a distintos aspectos:
- En relación con la maquinaria, las técnicas de organización sirven para Controlar el funcionamiento de las máquinas, departamentos; para saber el porcentaje de paradas y sus causas, para programar la carga de las máquinas, seleccionar nueva maquinaria, estudiar la distribución en planta, seleccionar los medios de transporte de materiales, estudiar y diseñar los equipos de trabajo, determinar los costes de mecanizado.
- En relación con el personal: Para determinar el número de operarios necesarios, establecer planes de trabajo, determinar y controlar los costes de mano de obra, como base de los incentivos directos, como base de los incentivos indirectos.
- En relación con el producto: Para comparar diseños, para establecer presupuestos, para programar procesos productivos, comparar métodos de trabajo, evitar paradas por falta de material.
- Otros aspectos: Para simplificar los problemas de dirección, aportando datos de interés que permiten resolver algunos de sus problemas, para mejorar las relaciones con los clientes al cumplirse plazos de entrega, para determinar la fecha de adquisición de los materiales o para eliminar los tiempos improductivos.
El buen funcionamiento de las empresas va a depender en muchas ocasiones de que las diversas actividades enunciadas estén correctamente resueltas y esto dependerá de la bondad de los tiempos calculados.
Además los tiempos calculados han de ser justos porque:
- De su duración depende lo que va a cobrar el operario, y lo que ha de pagar la empresa.
- Unos tiempos de trabajo mal calculados son el caldo de cultivo ideal para el nacimiento de la mayoría de los problemas laborales.
2.1.- Conceptos básicos.
Antes de explicar los diferentes sistemas de medición de tiempos es necesario que tengas claros los siguientes conceptos:
-
El tiempo de reloj (TR): es el tiempo que el operario está trabajando en la ejecución de la tarea encomendada y que se mide con el reloj. No se cuentan los paros realizados por el productor, tanto para atender sus necesidades personales como para descansar de la fatiga producida por el propio trabajo.
-
El factor de ritmo (FR): este concepto sirve para corregir las diferencias producidas al medir el TR, motivadas por existir operarios rápidos, normales y lentos, en la ejecución de la misma tarea.
El coeficiente corrector, FR, queda calculado al comparar el ritmo de trabajo desarrollado por el productor que realiza la tarea, con el que desarrollaría un operario capacitado normal, y conocedor de dicha tarea.
-
El tiempo normal (TN): es el TR de un operario capacitado, conocedor del trabajo y desarrollándolo a un ritmo "normal", emplearía en la ejecución de la tarea objeto del estudio. Su valor se determina al multiplicar TR por FR:
TN= TR x FR = Cte
y debe ser constante, por ser independiente del ritmo de trabajo que se ha empleado en su ejecución.
- Los suplementos de trabajo (K): como el operario no puede estar trabajando todo el tiempo de presencia en el taller, por ser humano, es preciso que realice algunas pausas que le permitan recuperarse de la fatiga producida por el propio trabajo y para atender sus necesidades personales. Estos periodos de inactividad, calculados según un suplemento de trabajo porcentual del TN se valoran según las características propias del trabajador y de las dificultades que presenta la ejecución de la tarea.
En la realidad, esos periodos de inactividad se producen cuando el operario lo desea:
Suplementos = TN x K = TR x FR x K
- El tiempo tipo (Tp): según la definición anteriormente establecida, el tiempo tipo está formado por dos sumandos: el tiempo normal y los suplementos. Es decir, es el tiempo necesario para que el trabajador capacitado y conocedor de la tarea, la realice a ritmo normal más los suplementos de interrupción necesarios, para que el citado operario descanse de la fatiga producida por el propio trabajo y pueda atender sus necesidades.
Existen muchos procedimientos distintos para medir los TR, valorar los FR, y determinar los K, no te debe extrañar que existan muchos sistemas para medir los tiempos tipo. En la industria se elige el que sea más económico, pues por un lado se encuentra el coste de su determinación y, por otro, la economía que le produce su exacta determinación.
Los sistemas más empleados para la medición de tiempos son los siguientes, que verás desarrollados más adelante:
- Estimación.
- Datos históricos.
- Muestreo.
- Tiempos predeterminados.
- Empleo de aparatos de medida.
Los dos primeros sistemas indicados son procedimientos no técnicos porque están basados en la experiencia profesional, su utilización es muy necesaria en la industria.
Autoevaluación
Solución
2.2.- Medición basada en datos históricos.
Esta técnica se fundamenta en la determinación de los tiempos a partir de los obtenidos en trabajos similares o a partir de los que pueden deducirse por comparación de otros ya conocidos.
Para medir el trabajo sobre la base de datos históricos, cada empleado o el supervisor registran el tiempo requerido para terminar cada trabajo. Por ejemplo, si el trabajo es perforar cierto tipo de agujero en 100 piezas, se registrará el tiempo por pieza. Posteriormente si el trabajo se realiza otra vez, se registrará también el tiempo por pieza y se compara con los datos anteriores. En esta forma, es posible mantener en control continuo el tiempo requerido por unidad de trabajo y controlar también las desviaciones del promedio histórico.
Sabiendo que la distribución de consecuencias de los tiempos empleados en realizar una misma tarea, siguiendo siempre el mismo método de trabajo, se agrupan según indica la estadística, será fácil, con los datos obtenidos, determinar los parámetros que definen la curva de distribución. No obstante, y debido a que los datos recopilados no tienen una gran precisión, el cálculo del tiempo se realiza calculando una media ponderada:
Siendo:
Tp, es el tiempo tipo.
To, es el tiempo óptimo registrado.
Tm, es el tiempo modal.
Ta, es el tiempo más abultado.
Se puede utilizar en los siguientes casos:
- Los métodos están claros. Imposibilidad de mejora de métodos.
- El producto que se fabrica no varía.
- No se han producido cambios tecnológicos u obsolescencias.
- Se tiene gran cantidad de datos sobre los procesos.
Este sistema no pretende una mejora y no permite la modificación de ningún elemento ya que los datos no serían válidos.
Ejercicio resuelto
Un trabajador de una fábrica de muebles lleva apuntados el tiempo que tarda en montar el modelo A, la lista es la siguiente:
Modelo realizado | A | A | A | A | A | A | A |
---|---|---|---|---|---|---|---|
Tiempo minutos | 3 | 5 | 4 | 7 | 4 | 2 | 4 |
2.3.- Medición basada en el muestreo.
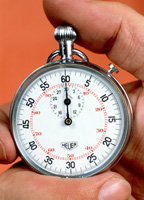
Este sistema se utiliza cuando hay que calcular los tiempos de gran número de tareas realizadas en puestos de trabajo diferentes. Para su ejecución práctica es preciso disponer de un reloj registrador de tiempo que te indique la hora de comienzo y de terminación de cada tarea.
La fórmula que determina el tiempo tipo por pieza es:
Siendo:
TE, es el tiempo empleado. Si en un puesto determinado de trabajo se producen n piezas, y se ha anotado con un reloj registrador, el comienzo y el fin de la tarea, la diferencia de esas dos lecturas te indica el tiempo empleado.
p, es el porcentaje medio que el operario está trabajando, determinado por muestreo. El analista de tiempos, al observar cada puesto de trabajo, debe anotar si el operario está trabajando o parado, el recuento de los datos tomados te permite calcular el porcentaje de tiempo que está trabajando o parado.
TE x p, se define como tiempo reloj (TR).
FR, es el factor de ritmo.
K, es el suplemento de descanso.
n, es el número de piezas que contiene el lote, cuyo tiempo se está midiendo.
El cálculo del tiempo tipo por pieza se reduce a determinar los valores que en cada puesto de trabajo tienen los factores de la fórmula:
Las ventajas de la utilización del sistema por muestreo son:
- Los analistas no necesitan estar tan formados, a menos que se quiera determinar tiempos tipo.
- No se interfiere tanto en la actividad de los operarios.
- El estudio se puede retrasar temporalmente sin que tenga un gran impacto en los resultados.
- Al realizar observaciones instantáneas durante un largo periodo, el trabajador casi no tiene posibilidad de variar los resultados de estudio.
- La duración del estudio es larga, minimizándose los efectos de las variaciones de corta duración.
Los inconvenientes del sistema son:
- En muchos casos no hay ningún registro del método usado por el operario.
- No es aconsejable para tareas de ciclo corto y repetitivas, en este caso, más aconsejable es el estudio de tiempos.
- Los trabajadores pueden cambiar su actividad intencionadamente cuando notan que están siendo observados.
- Si el analista no sigue las rutas y los momentos aleatorios establecidos el muestreo estará sesgado.
Autoevaluación
2.4.- Medición basada en tiempos predeterminados.
La utilización de sistemas de tiempos predeterminados para la obtención de los tiempos de ejecución de las operaciones limita la observación de las mismas al registro de los gestos necesarios para realizarlos sin proceder a medida alguna de tiempos. A partir de tablas en las que se dan los tiempos de ejecución de cada gesto, según tipo del mismo y ciertas características, se obtienen tiempos totales para cada operación compleja.
Para la determinación del tiempo normal de las operaciones base, además de los métodos descritos anteriormente, puede recurrirse a valores previamente establecidos, resultado de una minuciosa descomposición de las posibles operaciones globales en micromovimientos.
El sistema de tiempos predeterminados es una técnica de medición del trabajo en que se utilizan tiempos predeterminados para los movimientos humanos básicos (clasificados según su naturaleza y las condiciones en que se ejecutan) a fin de establecer el tiempo requerido de una tarea efectuada según una norma dada de ejecución.
La base de todo sistema de tiempos predeterminados es el hecho de que las variaciones del tiempo necesario para realizar un mismo movimiento son netamente pequeñas para diferentes operadores que hayan recibido un entrenamiento adecuado.
La mayoría de los sistemas se han realizado a través de miles de estudios de tiempos en situaciones controladas y se han establecido los tiempos para cada movimiento básico promediando todos los estudiados, lo cual hace que los datos sean muy fiables.
Los tiempos predeterminados se suelen obtener de los sistemas MTM (Methods Time Measurement), que se fundamentan en tiempos catalogados para cada tipo de movimiento, y nunca en la observación directa de valores tiempo-actividad.
El MTM descompone la tarea con mayor detalle que el que conseguimos con la técnica de datos normalizados y además es utilizable por las distintas empresas de un sector. La diferencia principal respecto al estudio de tiempos es que no altera las actividades productivas.
El cálculo del tiempo tipo de una tarea implicará seguir el siguiente procedimiento:
- Descomponer la tarea en micromovimientos o movimientos humanos básicos (alcanzar, coger, mover.).
- Consultar valores de tiempo que asignan las tablas de MTM a cada uno de dichos movimientos, con el fin de determinar los tiempos normales o básicos de cada micromovimiento mediante alguno de los sistemas disponibles.
- Sumar todos los tiempos normales o básicos obtenidos para determinar el tiempo de la tarea y añadir los suplementos correspondientes con el fin de calcular el tiempo tipo construido artificialmente.
Para saber más
Si tienes curiosidad por conocer más información de cómo funciona el sistema MTM en el enlace adjunto encontrarás la descripción del método y las explicaciones necesarias para poder calcular los tiempos.
2.5.- Diagramas de proceso.
Un diagrama de procesos muestra todas las operaciones necesarias para la realización de una tarea.
Para realizar un diagrama de procesos debes desglosar cada tarea en todas las operaciones en las que se divide. Mediante los escrutinios calcularás los tiempos normales de todas las operaciones y mediante el estudio del método de trabajo determinarás las frecuencias con las que se realiza cada operación. Con estos datos ya puedes saber cuál es el tiempo normal que se tarda en realizar una determinada tarea, este método te permite saber el tiempo invertido en realizar un producto en función de las características de este y del lote.
Una vez que tienes los tiempos normales de todas las operaciones debes saber cuál es la frecuencia con la que se repite en el ciclo dicha operación.
La frecuencia de una operación es la cantidad de veces que se realiza dicha operación dentro de un ciclo de trabajo.
Una vez que tengas los tiempos normales de las operaciones y sabiendo o calculando las frecuencias de cada operación estas en disposición de realizar un diagrama de proceso.
Se deben tener en cuenta todos los parámetros que influyen en la tarea, la parametrización de las tareas te permite ser más dinámico a la hora de plasmar los cambios que se producen en los procesos productivos.
Una vez realizado un diagrama de proceso para una tarea. Éste será fijo y aunque cambien los parámetros de los productos que se realizan en esa tarea, el diagrama será el mismo, solamente hará falta cambiar en el ordenador el parámetro que ha cambiado en la realidad y todos los tiempos y las frecuencias se recalcularán.
Debes conocer
La simbología utilizada para la representación gráfica de los acontecimientos que suceden puedes verla en la siguiente presentación:
Autoevaluación
Solución
2.6.- Diagrama de actividades simultáneas.
Se define este diagrama como la representación gráfica de la secuencia de elementos que componen las operaciones en que intervienen hombres y máquinas, y que permite conocer el tiempo empleado por cada uno, es decir, conocer el tiempo usado por los hombres y el utilizado por las máquinas.
Con base a este conocimiento se puede determinar la eficiencia de los hombres y de las máquinas con el fin de aprovecharlos al máximo.
Pasos para realizar el diagrama:
- Debes seleccionar la operación que será diagramada; se recomienda seleccionar operaciones importantes que pueden ser, costosas, repetitivas y que causan dificultades en el proceso.
- Determinar dónde empieza y dónde termina el ciclo que se quiere diagramar.
- Observar varias veces la operación, para dividirla en sus elementos e identificarlos claramente.
- Tomar los tiempos de los elementos de trabajo.
- Construcción del diagrama.
En el trabajo con máquinas automáticas o semiautomáticas, el personal que las opera permanece ocioso cuando la máquina está funcionando, por lo que sería conveniente asignarle durante su actividad alguna otra tarea o la operación de otras máquinas.
El diagrama te permite conocer las operaciones y tiempo del hombre, así como sus tiempos de ocio. Además se conocerá el tiempo de actividad o inactividad de su máquina, así como los tiempos de carga y descarga de la misma.
Para la construcción del diagrama lo primero que hay que seleccionar una distancia en cm. que represente la unidad de tiempo.
Se suele hacer a mano, en hojas de cuadrículas o en cualquier formato informático, preferiblemente Excel.
Cada cuadrícula representa una unidad de tiempo, para la elección de la unidad de tiempo se debe tener en cuenta el grado de detalle deseado.
Debes conocer
A continuación tienes un ejemplo de actividades simultáneas:
3.- Mejora de métodos.
Caso práctico
Fernando sigue dando vueltas a los procesos de fabricación que le han elaborado su sobrina y su amiga.
Por su experiencia cree que puede mejorar ese método para ahorrar tiempo y dinero, pero no sabe cómo hacerlo de una forma clara y ordenada, sin estropear el trabajo que ya han realizado.
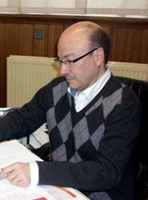
Un método de trabajo es la forma de realizar un trabajo, es decir, las pautas que se siguen en la realización de una tarea.
Debes saber que todo método puede mejorarse, para ello debes analizar el trabajo, anotar con exactitud todos los detalles del trabajo, tal como se ejecuta: transporte y manejo de materiales, trabajos ejecutados a máquina, trabajos ejecutados a mano.
Debes hacer el análisis en el mismo lugar de trabajo y preguntarte por cada detalle:
- ¿Por qué es necesario?
- ¿Cuál es el objeto?
- ¿Dónde debe hacerse?
- ¿Cuándo debe hacerse?
- ¿Quién es el más apto?
- ¿Cómo puede hacerse mejor?
Al realizarte estas preguntas debes tener en cuenta los materiales, máquinas, herramientas, estudio del producto, instalación de maquinarias, disposición del puesto de trabajo y seguridad, además de todas las consideraciones necesarias relativas a ese trabajo.
Para desarrollar el nuevo método de trabajo debes tener en cuenta las siguientes premisas:
- Eliminar los detalles innecesarios.
- Combinar cuanto sea posible las operaciones.
- Reordenar según una sucesión mejor.
- Simplificar todos los detalles necesarios.
- Hacer el trabajo fácil y seguro.
- Colocar anticipadamente los materiales y herramientas en los mejores sitios del área de trabajo.
- Usar el transporte por gravedad.
- Hacer trabajar ambas manos.
- Sostener las piezas con dispositivos.
- Desarrollar las ideas en colaboración.
- Poner por escrito el nuevo método, completándolo con croquis demostrativos.
Una vez hayas realizado el nuevo método completamente para aplicarlo debes conseguir la aceptación del operario que debe realizar el trabajo, el encargado y el jefe. Una vez aceptado se pone en marcha la ejecución del nuevo método y se usa hasta que se estudie otro mejor.
Es importante que escojas la forma y el momento más oportuno para la aplicación del nuevo método.
Autoevaluación
Solución
3.1.- Finalidad del estudio de métodos.
Es habitual que la dirección de una empresa recurra con frecuencia a especialistas o técnicos laborales que le ayuden a mejorar e incrementar la productividad del factor humano integrado en la actividad empresarial. Uno de los instrumentos más eficaces que se pueden utilizar para lograr ese objetivo es el estudio de trabajo, es decir, el examen y perfeccionamiento de las formas y secuencias en la ejecución de un determinado proceso de trabajo.
El estudio de trabajo se define como el examen sistemático de los métodos para realizar actividades con el fin de mejorar la utilización eficaz de los recursos y de establecer normas de rendimiento con respecto a las actividades que se están realizando. El estudio del trabajo resulta de gran utilidad y practicidad en las empresas debido a que:
- Es una forma de incrementar la productividad de una fábrica o instalación mediante la reorganización del trabajo, no requiriendo apenas desembolso de capital.
- Es un método sistemático lo que quiere decir que todos los pasos a aplicar son necesarios, no pudiendo saltarse ninguno de ellos.
- Es el método más exacto para el establecimiento de normas de rendimiento de las cuales depende la planificación y el control de la producción.
- Puede contribuir a la mejora de las condiciones de seguridad de los empleados al poner de manifiesto las operaciones de riesgo que existen y establecer unas formas más seguras de realizar esas mismas operaciones.
- Sus beneficios se producen de inmediato y continúan mientras el método mejorado se sigue aplicando.
- Es aplicable a las empresas de cualquier sector.
- Es de fácil aplicación y poco costoso, al pretender reorganizar de una manera más eficiente los recursos existentes y no realizar ninguna nueva adquisición o inversión que suponga desembolso de capital por parte de la empresa.
- Es un importante instrumento de investigación al alcance de la dirección de la empresa, ya que al detectar deficiencias salen a la luz otras que pueden estar relacionadas con las primeras.
La aplicación del estudio del trabajo requiere una serie de condiciones para obtener los resultados pretendidos; ésta, además de ser sistemática, debe ser continuada y generalizada, abarcar todos los extremos de la empresa llegando incluso a convertirse en una filosofía de la que participen y en la que crean todos los miembros de la organización.
El estudio del trabajo se compone de varias técnicas:
- Estudio de métodos: es el registro y examen crítico sistemáticos de los modos de realizar actividades con el fin de efectuar mejoras.
- Medición del trabajo: es la aplicación de técnicas para determinar el tiempo que invierte un trabajador cualificado en llevar a cabo una tarea según una norma de rendimiento preestablecida.
Autoevaluación
Solución
3.2.- Trabajo con máquinas.
Como imaginarás el tipo de trabajo que realiza un operario que trabaja con una máquina, no es igual al tipo de trabajo que se realiza sin maquinaria, por ello, debes diferenciar estos dos conceptos:
-
Trabajo libre: un trabajo se llama libre cuando no existe ninguna causa que limite a un operario la cantidad de trabajo a efectuar; al ser el trabajo libre se supone que la actividad realizada por el trabajador depende única y exclusivamente de él. Los trabajos libres son puramente manuales, como por ejemplo el ensamble de varias piezas de un cajón, o el ajuste de los herrajes para nivelar una puerta en un módulo de cocina.
-
Trabajo limitado: un trabajo es limitado cuando el trabajador que lo ejecuta no puede desplegar toda la capacidad de que es capaz, por alguna causa ajena a él, como puede ser la máquina que maneja o las características del propio trabajo, como por ejemplo el mecanizado de piezas mediante una calibradora.
Debes saber que por lo general, en los trabajos mecanizados suele ser la máquina la que marca el ritmo de trabajo del operario, es decir, limita las posibilidades de actividad del trabajador.
Cuando además un operario atiende varias máquinas, mientras está atendiendo una de ellas, pueden quedar paradas algunas de las máquinas restantes, hasta que el operario termine de atender la primera.
En esta situación el ciclo de las máquinas puede quedar alterado y la producción de las máquinas puede llegar a ser menor de la calculada en un primer momento. A este efecto se le llama INTERFERENCIA.
Las interferencias aumentan cuando aumenta el número de máquinas o el tiempo que se debe atender a las mimas.
Únicamente el incremento de la actividad del operario que atiende a las máquinas puede ayudar a disminuir el efecto de las interferencias.
3.2.1.- Cálculo de interferencias.
Los factores de trabajo y tiempo de maquinaria y operarios se pueden calcular. Para ello es preciso que primero tengas una idea clara de a qué se refiere cada concepto:
- Tiempo, T: expresado en minutos, el necesario para realizar una secuencia de actividad normal.
- Frecuencia, F: número de veces que se presenta cada secuencia por unidad de producción.
- Tiempo de trabajo con máquina en marcha del trabajador, MM: tiempo expresado en minutos, que se concede para realizar un trabajo o secuencia con la Máquina en Marcha a actividad normal.
- Tiempo de trabajo con máquina parada del trabajador, MP: igual que el tiempo de máquina en marcha, pero con la máquina parada.
- Cantidad de trabajo o tiempo tipo,
: es el tiempo que el trabajador está en funcionamiento.
- Tiempo de máquina, TM: tiempo que tarda la máquina en producir una unidad sin que haya ningún paro.
- Coeficiente Wright, X: actividad del operario si en el trabajo existe la posibilidad de interferencias.
- Número de máquinas asignadas, N.
- Actividad, A: su valor depende del tipo de actividad, cuando se habla de ciclo de trabajo óptimo o actividad 133, el valor de A será 1.33, cuando se habla actividad o ciclo de trabajo normal el valor de A será 1.00.
- Factor de interferencia correspondiente a una actividad, I: indica el tiempo de interferencia en tanto por uno de las máquinas paradas (MP).
- Ciclo normal, Ci(n): es la suma del tiempo de máquina más el tiempo de máquina parada.
- Ciclo óptimo, Ci(o):
- Saturación del operario, S:
- Producción normal hora, PN/H:
- Producción óptima hora, PO/H:
- Producción teórica hora, PT/H:
- Rendimiento de Servicio Normal, RSn: rendimiento exigible.
Aunque todo este lio de fórmulas te puede parecer muy complicado, en la página siguiente tienes un ejemplo resuelto que te hará ver cómo es más sencillo de lo que parece.
3.2.2.- Ejemplo de cálculo de interferencia.
A continuación tienes un problema ejemplo donde puedes ver cómo se utilizan las fórmulas explicadas en el apartado anterior.
Ejercicio resuelto
En un trabajo para la fabricación de sillas de madera, realizado con máquinas, se dispone de los siguientes datos:
- Tiempo de trabajo Máquina Parada = 3 minutos.
- Tiempo de trabajo Máquina Marcha= 0.90 minutos.
- Tiempo de máquina= 10 minutos.
- Máquinas existentes= 2.
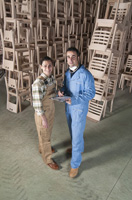
Autoevaluación
Solución
4.- Calidad en el proceso de producción.
Caso práctico
Ana y Clara, que se comprometieron a ayudarle con la organización de producción del pedido que había recibido, aún no han terminado su trabajo. Le advierten que tan importante como organizar bien la producción basándose en tiempos, es realizar un control de producción, vigilando que los procesos se realicen con calidad.
Para ello utilizarán distintas herramientas.
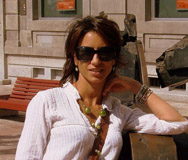
Una idea clara que tienes que tener es que las empresas son tan eficientes como lo son sus procesos. La mayoría de las empresas toma conciencia de esto y se plantean como mejorarlos y evitar algunos males habituales como: bajo rendimiento, poco enfoque al cliente, barreras departamentales, subprocesos inútiles debido a la falta de visión global del proceso.
La incorporación de las nuevas tecnologías de la información permite redefinir los procesos alcanzando grados de eficacia y eficiencia inimaginables hace algunos años.
Las empresas que sean capaces de descubrir estas posibilidades e implantarlas correctamente, conseguirán ventajas competitivas debido a la disminución de costes y el aumento de flexibilidad frente a los requerimientos de los clientes.
Los procesos de negocio deben estar correctamente gestionados empleando los sistemas de información para la gestión ERP (Enterprise Resource Planning). Un sistema de información para la gestión ERP se puede definir como una aplicación de gestión empresarial que integra el flujo de información, consiguiendo así mejorar los procesos en distintas áreas.
Los objetivos de los sistemas de planificación de recursos empresariales son:
- Optimización de los procesos empresariales.
- Acceso a información confiable, precisa y oportuna.
- La posibilidad de compartir información entre todos los componentes de la organización.
- Eliminación de datos y operaciones innecesarias.
- Reducción de tiempos y de los costes de los procesos.
4.1.- Control de calidad en los procesos.
La evolución del concepto de calidad en la industria y en los servicios te muestra que se está pasando de una etapa donde la calidad sólo se refería al control final, para separar los productos malos de los productos buenos, a una etapa de Control de Calidad en el proceso, con el lema "La Calidad no se controla, se fabrica".
Existen siete herramientas básicas que han sido ampliamente adoptadas en las actividades de mejora de la calidad y utilizadas como soporte para el análisis y solución de problemas operativos en la organización. En la industria existen controles o registros que podrían llamarse "herramientas para asegurar la calidad de una fábrica" como son:
- Hoja de control: es una hoja de recogida de datos que sirve para reunir y clasificar las informaciones, mediante la anotación y registro.
- Histograma: es la representación de una serie de medidas clasificadas y ordenadas.
- Diagrama de pareto: es una herramienta para priorizar los problemas o las causas que los genera.
- Diagrama de causa efecto: sirve para solventar problemas de calidad.
- Estratificación: es lo que clasifica la información recopilada sobre una característica de calidad.
- Diagrama de dispersión: es el estudio de dos variables que están relacionadas.
- Gráfica de control: se utilizan para estudiar la variación de un proceso y determinar a qué obedece esa variación.
La experiencia de los especialistas en la aplicación de estas herramientas señala que bien aplicadas y utilizando un método para la solución de problemas pueden ser capaces de resolver hasta el 95% de los problemas. En la práctica, estas herramientas requieren ser completadas con otras técnicas cualitativas y no cualitativas como son:
- La lluvia de ideas.
- La encuesta.
- La entrevista.
- Diagrama de flujo.
- Matriz de selección de problemas.
Las siete herramientas sirven para:
- Detectar problemas.
- Delimitar el área problemática.
- Estimar factores que probablemente provoquen el problema.
- Determinar si el efecto tomado como problema es verdadero o no.
- Prevenir errores debido a omisión, rapidez o descuido.
- Confirmar los efectos de mejora.
- Detectar desfases.
Autoevaluación
Solución
4.2.- Gráficos de control (I).
Los gráficos de control o cartas de control son una importante herramienta utilizada en el control de calidad de procesos. Básicamente, una Carta de Control es un gráfico en el cual se representan los valores de algún tipo de medición realizada durante el funcionamiento de un proceso continuo, y que sirve para controlar dicho proceso.
Por ejemplo, supón que tienes una máquina regruesadora que tiene que dejar las piezas de con un espesor de 10 cm, si la pieza de madera es demasiado delgada será deficiente, si la pieza es demasiado gruesa será excesiva. Entonces, en el lugar de salida de las piezas, hay un operario que cada 30 minutos toma una, mide su grosor y registra la observación.
Piezas | 1 | 2 | 3 | 4 | 5 | 6 | 7 | 8 | 9 | 10 |
---|---|---|---|---|---|---|---|---|---|---|
Espesor (cm) | 10.1 | 9.90 | 9.95 | 10.22 | 9.89 | 10.1 | 10.2 | 9.95 | 9.80 | 10.00 |
Puedes observar una línea quebrada irregular, que te muestra las fluctuaciones del espesor de la pieza a lo largo del tiempo. Esta es la fluctuación esperable y natural del proceso. Los valores se mueven alrededor de un valor central, la mayor parte del tiempo, cerca del mismo. Pero en algún momento puede ocurrir que aparezca uno o más valores demasiado alejados del promedio. ¿Cómo puedes distinguir si esto se produce por la fluctuación natural del proceso o porque el mismo ya no está funcionando bien? Esta es la respuesta que provee el control estadístico de procesos, y a continuación verás cómo lo hace.
Todo proceso de fabricación funciona bajo ciertas condiciones o variables que son establecidas por las personas que lo manejan para lograr una producción satisfactoria. Todo proceso de fabricación resulta de la concurrencia de varios factores que definen al proceso, con el fin de obtener el producto deseado.
Cada uno de estos factores está sujeto a variaciones que realizan aportes más o menos significativos a la fluctuación de las características del producto, durante el proceso de fabricación. Los responsables del funcionamiento del proceso de fabricación fijan los valores de algunas de estas variables, que se denominan variables controlables. Por ejemplo, en el caso de la engruesadora se fija el espesor, la velocidad de trabajo, la presión, la materia prima que se utiliza. Pero un proceso de fabricación es una suma compleja de eventos grandes y pequeños.
Existe una gran cantidad de variables que sería imposible o muy difícil controlar. Estas se denominan variables no controlables. Por ejemplo, pequeñas variaciones de calidad de la madera, pequeños cambios de velocidad en la máquina, ligeras fluctuaciones de la corriente eléctrica que alimenta la máquina.
4.2.1.- Gráficos de control (II).
Los efectos que producen las variables no controlables son aleatorios. Además, la contribución de cada una de las variables no controlables a la variabilidad total es cuantitativamente pequeña.
Son variables no controlables las responsables de la variabilidad de las características de calidad del producto. Los cambios en las variables controlables se denominan Causas Asignables de variación de proceso, porque es posible identificarlas.
Causas Asignables: son causas que pueden ser identificadas y que conviene descubrir y eliminar, por ejemplo, un fallo de la máquina por desgaste de una pieza, un cambio muy notorio en la calidad de la madera. Estas causas provocan que el proceso no funcione como se desea y por lo tanto es necesario eliminar la causa, y retornar el proceso a un funcionamiento correcto.
Causas no Asignables: son una multitud de causas no identificadas, ya sea por falta de medios técnicos o porque no es económico hacerlo, cada una de las cuales ejerce un pequeño efecto en la variación total. Son inherentes al proceso mismo, y no pueden ser reducidas o eliminadas a menos que se modifique el proceso.
Cuando el proceso trabaja afectado solamente por un sistema constante de variables aleatorias no controlables (Causas no asignables) se dice que está funcionando bajo Control Estadístico. Cuando además de las causas no asignables, aparece una o varias causas asignables, se dice que el proceso está fuera de control.
El uso del control estadístico de procesos lleva implícitas algunas hipótesis, que tienes descritas a continuación:
Una vez que el proceso está en funcionamiento bajo condiciones establecidas, se supone que la variabilidad de los resultados en la medición de una característica de calidad del producto se debe sólo a un sistema de causas aleatorias, que es inherente a cada proceso en particular.
- El sistema de causas aleatorias que actúa sobre el proceso genera un universo hipotético de observaciones que tiene una Distribución Normal.
- Cuando aparece alguna causa asignable provocando desviaciones adicionales en los resultados del proceso, se dice que el proceso está fuera de control.
La función del control estadístico de procesos es comprobar en forma permanente si los resultados que van surgiendo de las mediciones están de acuerdo con las dos primeras hipótesis. Si aparecen uno o varios resultados que contradicen o se oponen a las mismas, es necesario detener el proceso, encontrar las causas por las cuales el proceso se apartó de su funcionamiento habitual y corregirlas.
Autoevaluación
Solución
Anexo.- Licencias de recursos.
Recurso (1) | Datos del recurso (1) | Recurso (2) | Datos del recurso (2) |
---|---|---|---|
![]() |
Autoría: Latinstock. Licencia: Uso Educativo no comercial para plataformas de FPaD. Procedencia: Latinstock código: 42-24516337. |
![]() |
Autoría: Photodisc. Licencia: Uso Educativo no comercial para plataformas de FPaD. Procedencia: CD-DVD Num. V07. |
![]() |
Autoría: Latinstock. Licencia: Uso Educativo no comercial para plataformas de FPaD. Procedencia: Latinstock código: TI0700831. |
![]() |
Autoría: Latinstock. Licencia: Uso Educativo no comercial para plataformas de FPaD. Procedencia: Latinstock código: 42-22991809. |
![]() |
Autoría: Latinstock. Licencia: Uso Educativo no comercial para plataformas de FPaD. Procedencia: Latinstock código: 29053. |
![]() |
Autoría: Stockbyte. Licencia: Uso Educativo no comercial para plataformas de FPaD. Procedencia: CD-DVD Num. CD109. |
![]() |
Autoría: Latinstock. Licencia: Uso Educativo no comercial para plataformas de FPaD. Procedencia: Latinstock código: IS482-022. |
![]() |
Autoría: Photodisc. Licencia: Uso Educativo no comercial para plataformas de FPaD. Procedencia: CD-DVD Num. V07. |
![]() |
Autoría: Latinstock. Licencia: Uso Educativo no comercial para plataformas de FPaD. Procedencia: Latinstock código: TI4100056. |
![]() |
Autoría: Latinstock. Licencia: Uso Educativo no comercial para plataformas de FPaD. Procedencia: Latinstock código: BLD054558. |
![]() |
Autoría: Latinstock. Licencia: Uso Educativo no comercial para plataformas de FPaD. Procedencia: Latinstock código: CB0506ADH0595. |
![]() |
Autoría: Photodisc. Licencia: Uso Educativo no comercial para plataformas públicas de FPaD. Procedencia: CD-DVD Num. V07. |
![]() |
Autoría: Latinstock. Licencia: Uso Educativo no comercial para plataformas de FPaD. Procedencia: Latinstock código: WESTF11038. |
![]() |
Autoría: Latinstock. Licencia: Uso Educativo no comercial para plataformas de FPaD. Procedencia: Latinstock código: 26060. |
![]() |
Autoría: Latinstock. Licencia: Uso Educativo no comercial para plataformas de FPaD. Procedencia: Latinstock código: 42-22936035. |
![]() |
Autoría: Latinstock. Licencia: Uso Educativo no comercial para plataformas de FPaD. Procedencia: Latinstock código: FAN2016413. |
![]() |
Autoría: Photodisc. Licencia: Uso Educativo no comercial para plataformas de FPaD. Procedencia: CD-DVD Num. V07. |