Caso práctico
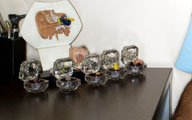
PROPIEDADES DE LOS MATERIALES DE IMPRESIÓN
Los materiales para la toma de impresión se componen de dos elementos: una sustancia base y un catalizador, los cuales debes mezclar según las proporciones indicadas por el fabricante. Los materiales una vez preparados se diferencian en sus propiedades físicas. Las propiedades más importantes son la viscosidad, la estabilidad dimensional de la impresión terminada y la dureza final.
TIPOS DE MATERIALES
Existen dos tipos de materiales para la toma de impresiones de oído: el acrílico, actualmente en desuso y las siliconas.
Sustancia o agente acelerador de una reacción química, en algunos casos también puede configurarse como un agente iniciador de la reacción.