- Ausencia de tensión en la red:
Antes de proceder a la comprobación de una máquina que no funciona, debemos asegurarnos de que le llega corriente. Para ello primero comprobamos si hay pilotos apagados y comprobamos la tensión a la entrada con un voltímetro.
La mayoría de los motores tiene una protección por guardamotor. Si hay ausencia de corriente, los guardamotores se desconectan y cuando se restaura la tensión, debemos volver a pulsar el pulsador de marcha para que vuelva a funcionar la máquina.
Si la máquina está protegida por interruptores magnetotérmicos y falla la corriente, la máquina parará, pero al restaurarse la corriente el motor se pondrá en marcha por sí solo. Esta marcha inmediata puede suponer un peligro para la máquina, por lo que algunas incluyen dispositivos que impiden que la máquina pueda volver a funcionar por sí sola.
En algunas ocasiones la ausencia de corriente no se debe a una avería, sino que ha sucedido porque por alguna razón puntual han saltado las protecciones. Incluso hay algunas ocasiones en que la máquina ha sido desenchufada accidentalmente y nadie se ha percatado de algo tan simple como esto.
- Fusibles fundidos por sobrecarga:
Existen dos lugares en los que generalmente hay fusibles en una instalación eléctrica:
- En una línea de suministro en la cabecera de la red, antes de los interruptores automáticos.
- Dentro de la máquina, en las inmediaciones a la entrada del cable de alimentación.
En cualquiera de los dos casos, la reparación consiste en colocar un fusible del mismo amperaje del fundido, nunca se debe de aumentar su calibre. Una sobredimensión de los fusibles supone una desprotección de la línea o maquinaria, que llevaría a su destrucción.
Cuando una línea de suministro funde sus fusibles con demasiada frecuencia, la solución puede ser aumentar la sección de la línea, o hacer una contratación de suministro de mayor potencia. Otras soluciones pueden ser hacer más derivaciones y revisar la adecuación de las protecciones magnetotérmicas.
- Fusibles fundidos por cortocircuito:
Cuando se funde un fusible, generalmente no sabemos si ha sido por una sobrecarga o por un cortocircuito. Si se produce por cortocircuito, cuando se coloque el fusible de repuesto éste volverá a fundirse de inmediato, mientras que si ha sido por sobrecarga y la sobrecarga persiste, el fusible de repuesto tardará algún tiempo en volver a fundirse.
En caso de que se haya fundido por cortocircuito debe procederse como se describe en un apartado posterior "Localización y reparación de averías en circuitos eléctricos", abriendo los interruptores y volviéndolos a cerrar uno a uno hasta localizar el sector en cortocircuito. Una vez localizado el sector con fallo, se puede restablecer el servicio en las otras líneas y reparar la parte dañada.
- Cable de alimentación cortado:
Este tipo de averías sólo se suele producir en cables flexibles de alimentación a pequeños receptores. El corte de los cables suele producirse en los extremos, y casi nunca en el centro.
- Borne suelto:
Suele ocurrir que los bornes se aflojan una vez transcurrido un tiempo de uso, sobre todo cuando hay más de un conductor en el mismo borne. Se detecta esta avería por la falta de una fase en el receptor, pero también podemos detectarlo fácilmente por el color que toma el material aislante del borne e incluso la punta de los cables. Este defecto incluso puede producir el incendio del cuadro.
Apretar el borne casi nunca es la solución, ya que durante la falta de contacto se puede producir un chisporroteo que consume el cable y deteriora los aislantes. Cuando se trata de un borne de conexión la solución es cambiar el borne, pero cuando se trata de un magnetotérmico no se disponen de conjuntos de repuestos de este tipo y hay que cambiar el interruptor completo.
- Fallo de aislamiento en la instalación interior y el diferencial salta:
Cuando salta un diferencial, lo habitual es que podamos volver a reestablecer el servicio sin dificultad, pero si esto no sucede, es que existe una avería en algún receptor en concreto. El procedimiento para localizar el circuito con fallo es el mismo que para localizar un cortocircuito: desconectar todos los receptores, conectar el diferencial y enchufar de nuevo, uno a uno, cada receptor, hasta localizar el averiado.
Hay veces que el diferencial salta con un receptor, y otras con otro receptor distinto; en estos casos debemos buscar la avería en la línea, en humedades que penetran por las cajas de empalme y síntomas que solo aparecen cuando llueve, en bases de enchufe grasientas, etc.
Algunas veces los diferenciales normales saltan de forma intempestiva cuando utilizamos varios receptores que emplean fuentes internas de rectificación de la corriente (como ordenadores, televisores, etc.). La solución en estos casos puede ser colocar diferenciales especiales "superinmunizados" que soporten los picos de corriente que se producen en este tipo de receptores, o repartir entre varias fases estos receptores.
Lo que nunca debemos hacer es anular el diferencial, puentearlo o quitarlo.
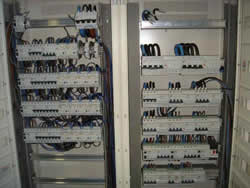
Cuando mediante cables se permite el paso de la electricidad, como cuando cargas la batería de un vehículo desde otro.