U.T. 2.- Programación CNC ISO. Taladrado.
Caso práctico
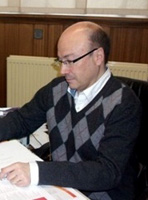
El tío Fernando, finalmente, se ha convencido a comprar la máquina CNC de 5 ejes, ya que así podrá hacer todos los mecanizados posibles tanto en 2 como en 3 dimensiones. Lo primero que se da cuenta es que aunque hay máquinas con configuraciones "de serie", normalmente cada cliente le solicita al fabricante de la máquina los porta-brocas para realizar los mecanizados que requiere, el numero de herramientas que puede llevar el almacén para realizar los fresados o las dimensiones de la zona de trabajo de la máquina que definen las medidas de las piezas a mecanizar. Una vez realizado el estudio de necesidades y tras el análisis junto a proveedores que tienen máquina CNC ya se ha decidido por las características que cree que mejor se adaptan a sus necesidades, tanto presentes como futuras, encargando para ello el grupo de taladro y el grupo de fresado que más le interesa.
Aunque a Fernando le parece mucho dinero y cree que con una máquina de 3 ejes bastaría para su empresa, accede a comprar una de 5 ejes.
Una vez realizado el encargo, el fabricante la servirá a la empresa de Fernando en unos pocos días. Como es una máquina con la que nunca ha trabajado y tiene que aprender su manejo y a elaborar los programas para fabricar las piezas, el fabricante de la máquina les dará un curso de una semana para enseñarle su manejo.
Materiales formativos de FP Online propiedad del Ministerio de Educación y Formación Profesional.