Además de los compresores alternativos, que suponen el 90% de los compresores utilizados en máquinas frigoríficas, existen otros tipos de compresores que se emplean en situaciones singulares: grandes potencias, necesidad de menor ruido, grandes presiones, etc.
Compresor scroll
En las imágenes puedes observar como el fluido refrigerante entra en el sistema de espirales por la periferia de las mismas. Ese volumen de refrigerante es desplazado y comprimido, debido al giro de la excéntrica hacia el centro del sistema. En ese traslado el volumen de la cámara va disminuyendo, lo que provoca el aumento de la presión y el calentamiento del gas refrigerante. Por último al llegar al centro de las espirales se encuentra con el orificio de descarga y sale del compresor.
Este tipo de compresores presentan ventajas frente a los alternativos. Al tener un número de piezas móviles muy pequeño sufren menos averías. La inexistencia de juntas y segmentos en los compresores scroll, hace que las pérdidas mecánicas por rozamiento en este tipo de compresores sean menores. Tampoco existe el espacio muerto en la cabeza del pistón por lo que el rendimiento volumétrico mejora. Por último son muy silenciosos y prácticamente no tienen vibraciones. Como desventajas presentan un mantenimiento más complejo en caso de avería y un tamaño mínimo mayor que los alternativos. Son más caros que los alternativos. Como todos los compresores, hay que hacerlo trabajar en el punto de mayor rendimiento y, en estas condiciones, tienen rendimientos superiores (EER) a los compresores alternativos.
Compresores de tornillo
Estos compresores son para grandes potencias y presiones, aunque actualmente se pueden encontrar compresores de tan sólo 2 kW. Es un compresor helicoidal de dos rotores, más conocido por compresor de tornillo. Es una máquina rotativa en la que la compresión del vapor se efectúa mediante dos rotores. El motor actúa sobre uno de ellos, el conductor y el otro, el conducido, gira por acción del primero.
El compresor de tornillo presenta una serie de ventajas frente al compresor alternativo. Por un lado su vida útil es mayor dado que no tiene tantas piezas móviles. Esto también redunda en un menor mantenimiento. No son tan sensibles a los golpes de líquido por lo que el sobrecalentamiento puede disminuirse, lo que supone un ahorro de energía. Al no tener pistones no existe el espacio muerto en los cilindros y el rendimiento volumétrico es mayor. Este tipo de compresor es el que mejor se puede regular (de forma lineal desde el 10% hasta el 100%), esta regulación se lleva a cabo con un pistón de capacidad que abre o cierra el espacio entre los dos tornillos. Como inconvenientes tienen que son más costosos y ruidosos que los alternativos. También, al ser las tolerancias muy reducidas la gestión del aceite es más crítica.
Compresores centrífugos
Si te fijas en la clasificación que hemos hecho al principio de la unidad, los compresores centrífugos son un tipo completamente diferente de compresores. En éstos, la compresión se realiza mediante la fuerza tangencial engendrada por un rodete que gira dentro de una carcasa y actúa sobre las moléculas de fluido. Este tipo de compresores están íntimamente relacionados con las bombas y los ventiladores. Vamos a ver dos tipos:
Compresores centrífugos de flujo radial. Estos aparatos centrífugos se crearon para obtener grandes capacidades de enfriamiento, y constan principalmente de un compresor centrífugo, impulsado por un motor eléctrico. El compresor centrífugo se fundamenta esencialmente en uno o varios rodetes montados sobre un eje y encerrados en una cubierta de hierro fundido. El número de rodetes que se puede ensamblar depende principalmente de la magnitud de la presión que queremos desarrollar. Los compresores centrífugos son turbo-máquinas o máquinas generadoras de flujo continuo. Las velocidades rotatorias comunes varían entre 3 000 y 8 000 rpm, pudiendo llegar a velocidades más altas.
El funcionamiento es muy similar a los ventiladores centrífugos radiales. En la siguiente animación podemos ver un compresor centrífugo radial en una aplicación diferente de la máquina frigorífica:
Compresores centrífugos de flujo axial. Los compresores de flujo axial son compresores rotativos dinámicos que utilizan conjuntos de planos aerodinámicos en forma de abanico para comprimir progresivamente el fluido de trabajo. El conjunto de los planos aerodinámicos se disponen en filas, por lo general en parejas: una es rotativa y la otra fija. Los planos de rotación, llamados rotores, aceleran el fluido. Las planos fijos, llamados estatores, desaceleran y redirigen la dirección del flujo del fluido preparándolo para las palas del rotor de la etapa siguiente.
Los compresores axiales son casi siempre de múltiples etapas. El área de la sección transversal del paso de gas disminuye a lo largo del compresor para mantener una velocidad adecuada. Los compresores de más de 5 etapas o con una relación de presión 4:1, son generalmente de geometría variable.
Los compresores axiales alcanzan altos rendimientos, alrededor del 90%. Sin embargo, son relativamente caros, ya que tienen un gran número de componentes, las tolerancias son muy ajustadas y materiales son de alta calidad. Se utilizan para grandes caudales. Observa la animación del funcionamiento de un compresor mixto axial-radial, en el que hay un sistema de enfriamiento del gas entre las dos etapas de compresión (axial en primer lugar y radial en segunda etapa). Al bajar la temperatura del gas, el rendimiento aumenta.
Otros compresores rotativos
Dentro de los compresores rotativos existen otras variedades que vamos a ver a continuación.
Compresor de paletas. En este compresor el eje motor hace girar el rotor de forma excéntrica respecto del estátor. Del rotor salen unas paletas que llegan hasta el estator impulsadas por un muelle. Observa la animación siguiente. Se trata de un compresor de 8 paletas. Hay otros modelos que tienen 1, 2, 4, 8 o 10. El fluido accede al compresor desde la derecha de la animación llenando una cámara que se crea entre dos paletas y la carcasa del compresor. El giro de eje hace que el volumen de la celda vaya disminuyendo hasta la descarga del refrigerante que se hace por la derecha. Como puedes ver dentro del compresor hay una gran aportación de aceite para reducir el rozamiento. En la descarga el gas refrigerante que lleva aceite en suspensión pasa por un filtro de aceite, que recoge el sobrante de aceite y lo retorna al cárter. El proceso es continuo. El problema de estos compresores es la estanqueidad y el rozamiento con las paredes, lo que lo hace útil únicamente para bajas presiones. El rozamiento de las paredes se evita con un sistema de lubricación como el que se ve en la imagen;
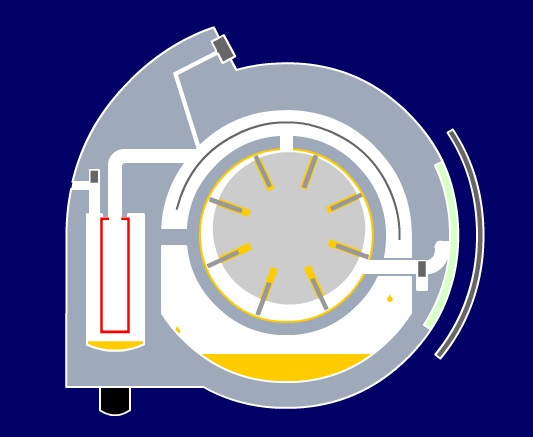
Compresor lobular o Roots. Como puedes ver en la siguiente animación, el compresor lobular lleva dos ejes que transmiten el movimiento a dos rotores en forma de ocho. Estos rotores están en todo momento en contacto entre ellos y con las paredes del estator separando la aspiración de la descarga. La geometría hace que el volumen se reduzca progresivamente, lo que implica un aumento de la presión y temperatura del refrigerante. La transición del refrigerante no es tan continua como en los casos anteriores sino que tienen unas pulsaciones más acentuadas. Este tipo de compresor se emplea para pequeñas compresiones.
Una turbina radial es una turbomáquina en la que el flujo del fluido de trabajo es radial al eje de rotación.